High-Quality Horizontal Corrugation Machine for 0.18-0.35mm Corrugated Sheets
By:Admin
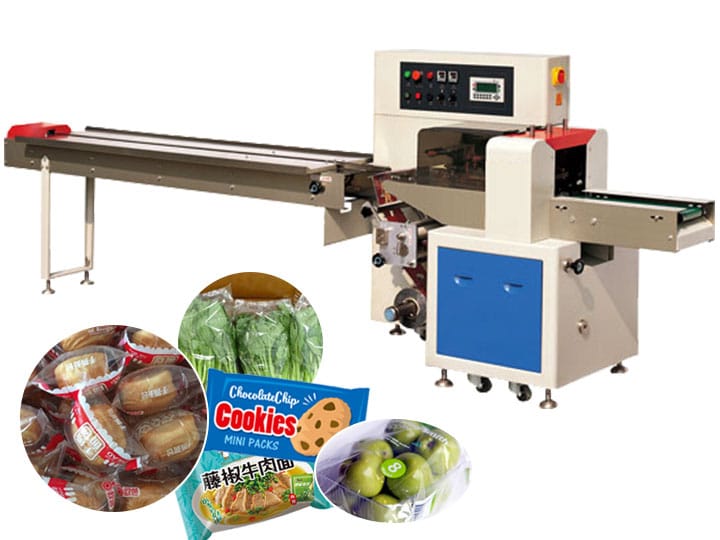
G550 Barrel Corrugation Machine – A Perfect Solution for 0.18-0.35mm Corrugated Sheets
Corrugated sheets are widely used in the construction industry for roofing, cladding, and facades due to their high durability and strength. The manufacturing process of corrugated sheets involves horizontal corrugation of metal sheets, which requires a high-quality machine that can form corrugations precisely. The G550 Barrel Corrugation Machine is one such machine that can cater to the needs of the corrugated sheet manufacturing industry.
The G550 Barrel Corrugation Machine is a horizontal corrugation machine that can form 0.18-0.35mm corrugated sheets with high precision and accuracy. The machine has been manufactured using advanced technology, which ensures that it delivers excellent results with minimal maintenance. The machine can be used to manufacture corrugated sheets of various sizes, making it a versatile solution for the corrugated sheet industry.
One of the key features of the G550 Barrel Corrugation Machine is its robustness. The machine is made of high-quality materials that are designed to withstand the rigors of continuous use. The machine has a sturdy frame that provides stability and ensures that the corrugated sheets are formed accurately. The machine is also equipped with a powerful motor that can deliver high torque, which is essential for the smooth functioning of the machine.
The G550 Barrel Corrugation Machine is also easy to operate, which makes it an ideal solution for small-scale manufacturers. The machine has a user-friendly interface that allows operators to control the machine easily. It also comes with a range of safety features that ensures that the operator is safe while using the machine.
Another advantage of the G550 Barrel Corrugation Machine is that it is low maintenance. The machine has been designed with minimal moving parts, which means that there is less wear and tear. The machine also comes with a range of maintenance features that make it easy to clean and service.
In conclusion, the G550 Barrel Corrugation Machine is an excellent solution for the corrugated sheet manufacturing industry. Its robustness, precision, ease of use, and low maintenance make it a perfect fit for small and medium-scale manufacturers. If you are looking for a high-quality horizontal corrugation machine, the G550 Barrel Corrugation Machine is the perfect choice.
Keywords: Horizontal Corrugated Sheet Profiling Machine, G550 Barrel Corrugation Machine.
Company News & Blog
Unveiling the Charm of Timeless Elegance in THAMRONGCHAI's Terrazzo
Terrazzo flooring has been a favorite choice for architects and designers for centuries. Its timeless elegance and durability make it the perfect choice for both residential and commercial spaces. One such company that excels in delivering exquisite Terrazzo flooring is Machi Terrazzo.Founded in 1988, Machi Terrazzo has been a leading provider of Terrazzo flooring services for over three decades. The company specializes in creating unique and customized Terrazzo floors that add significant value to any space. Their skilled workforce and state-of-the-art machinery ensure that every floor is a masterpiece in itself.Machi Terrazzo offers a wide range of Terrazzo flooring materials, including marble, granite, quartz, and glass chips. The company uses high-quality materials sourced from the best suppliers to ensure that every project is executed to perfection. They also offer personalized design and installation services to their clients, making them a one-stop-shop for all Terrazzo flooring needs.One of the standout features of Machi Terrazzo's services is their attention to detail. Every project is executed with utmost care and precision. The company aims to exceed their clients' expectations in terms of quality and service, making them a trusted choice for many architects, designers, and property owners.Machi Terrazzo's team of experts use a combination of traditional and modern techniques to create stunning Terrazzo floors. They use state-of-the-art machinery to ensure precise cutting and polishing. Their highly experienced workforce creates intricate designs that are unique to every space.Apart from being aesthetically pleasing, Terrazzo flooring offers several advantages. It is highly durable and requires minimal maintenance, making it an excellent choice for high-traffic areas. It is also stain-resistant, corrosion-resistant, and fire-resistant, making it a safe and practical flooring option. These features, together with the timeless elegance of Terrazzo, make it a wise investment for any property owner.In conclusion, Machi Terrazzo is a top-notch provider of Terrazzo flooring services. Their commitment to quality, attention to detail, and comprehensive service offerings make them an industry leader. If you're looking to add a touch of elegance and durability to your home or office space, consider the services of Machi Terrazzo. With their team of experts and top-notch materials, you're sure to get a flooring solution that exceeds your expectations.
Highly Efficient Slitter with Razor and Rotating Knife Cutting Systems for Flexible and Rigid Materials, 1300mm Width
Title: Slitter - BRASIA LTDA Introduces 1300 mm Wide Automatic Roll Slitter for Versatile Material CuttingSubtitle: Cutting-Edge Technology Enhances Precision and Efficiency in Material Processing[date][City], [Country] – Slitter - BRASIA LTDA, a leading provider of innovative cutting solutions, has recently unveiled its latest offering, an advanced 1300 mm wide Automatic Roll Slitter. With its exceptional razor and rotating knife cutting systems, this versatile machine is capable of handling a wide range of flexible and rigid materials, empowering industries with enhanced productivity and precision.1- Efficient Cutting of Flexible Materials:Equipped with a razor cutting system and special articulated support, the 1300 mm Automatic Roll Slitter is specifically designed to cater to the cutting needs of flexible materials. From BOPP, PP, PE, PVC, to non-printed materials, this cutting-edge machine ensures clean and precise cuts, enhancing the efficiency of production processes.2- Seamless Cutting of Rigid and Semi-Rigid Materials:In addition to its razor cutting system, this innovative slitter also features a rotating knife cutting system. This unique capability enables the machine to effortlessly handle rigid and semi-rigid materials such as card paper, cardboard, stamped paper, felt, and laminated materials, expanding its application across various industries.3- Wide Roll Entry and Smooth Alignment:The 1300 mm Automatic Roll Slitter boasts a spacious roll entry point with a diameter of 1000 mm. This not only allows for easy loading and unloading of materials but also ensures smooth alignment, minimizing downtime during operation. The inclusion of an aligner, air shaft, and electromagnetic control further optimizes the slitting process.4- Enhanced Output and Control:To maximize productivity, the slitter is equipped with double articulated air shafts, ensuring efficient winding of slit materials. With individual electromagnetic control, operators have precise control over the winding process, preventing any potential material damage or inconsistency.5- Accurate Reading with Electric Photo Cell:Incorporating cutting-edge technology, the 1300 mm Automatic Roll Slitter is equipped with an electric photo cell. This feature enables the machine to accurately read lengthwise printing, allowing for precise cutting based on specific patterns or designs.6- Convenient Meter Counter:This sophisticated slitter also features a meter counter with an electronic sensor. This enables operators to track the length of materials being processed, ensuring precise measurements and reducing waste.7- Advanced Automatic Stop Sensor:The Automatic Roll Slitter is designed with an automatic stop sensor, which halts the machine upon completion of the programmed measurement. This ensures optimal efficiency and prevents any potential material waste.8- Speed Control at Your Fingertips:To cater to diverse processing needs, this state-of-the-art slitter offers speed control through digital programming. Operators can easily adjust the cutting speed to meet the requirements of different materials, providing versatility and convenience.9- User-Friendly Digital Control Panel:All operational functions of the 1300 mm Automatic Roll Slitter are effortlessly programmed using a digital control panel. With programmed memory functions, users can conveniently store and recall specific settings, streamlining the overall production process.Slitter - BRASIA LTDA's new 1300 mm Automatic Roll Slitter represents a significant advancement in material cutting technology. Its superior cutting systems, precise controls, and user-friendly features make it an unrivaled choice for industries seeking to enhance productivity, streamline processes, and achieve impeccable cutting results.For more information on the 1300 mm Automatic Roll Slitter and its wide range of applications, please contact:[Contact Information]About Slitter - BRASIA LTDA:Slitter - BRASIA LTDA specializes in the development and production of advanced cutting solutions. With a commitment to innovation, reliability, and customer satisfaction, the company has established itself as a trusted provider of cutting-edge technologies in the industry.
China Manufacturers & Suppliers of High-Quality Wall And Roof Panel Roll Forming Machines
Wall Panel Roll Forming Machine: A Game-Changer in Construction IndustryIn the fast-paced construction industry, efficiency and quality play a crucial role. This is where the Wall Panel Roll Forming Machine steps in as a game-changer. Taking China by storm, this innovative machine has gained popularity among manufacturers and contractors, revolutionizing the way wall panels are produced.With the growing demand for energy-efficient and eco-friendly buildings, wall panels have become an integral part of modern construction projects. Traditional construction methods, such as bricklaying and concrete casting, can be time-consuming, labor-intensive, and costly. This is where roll forming technology has stepped in to provide an efficient and economical solution.Wall Panel Roll Forming Machine, developed and manufactured by leading Chinese manufacturers, provides a seamless production process for wall panels. Equipped with advanced technology and precision engineering, this machine enables manufacturers to produce high-quality panels in large quantities within a short period.So, what exactly is a Wall Panel Roll Forming Machine? It is a production line that consists of a series of rollers, forming stations, and cutting systems. It takes raw materials, such as galvanized steel or aluminum coils, and shapes them into precise and uniform profiles. These profiles can be customized according to specific design requirements, including thickness, width, and length.The Wall Panel Roll Forming Machine offers numerous advantages over conventional manufacturing methods. Firstly, it significantly reduces labor costs and human errors. The automated process ensures consistent panel dimensions and eliminates the need for manual intervention, resulting in a fast and efficient production line.Secondly, the Wall Panel Roll Forming Machine optimizes material usage, reducing waste and saving costs. By precisely controlling the amount of raw material fed into the machine and its shaping process, manufacturers can minimize scrap and maximize panel output.Furthermore, this machine allows for customization and flexibility. With adjustable roller stations, manufacturers can create various panel profiles, including flat, corrugated, or trapezoidal shapes, to meet diverse construction needs. This versatility enables architects and designers to unleash their creativity and bring unique architectural visions to life.In addition, the Wall Panel Roll Forming Machine enhances safety on construction sites. With panels produced using this technology, the risk of accidents, such as falling debris or collapses, is minimized. These panels are lightweight yet structurally robust, offering enhanced durability and improved seismic resistance.Lastly, the Wall Panel Roll Forming Machine contributes to green construction practices. By using environmentally friendly materials, such as recyclable metals, and reducing energy consumption through efficient production processes, it supports sustainable building practices. Furthermore, its precision engineering ensures tight joints and insulation, enhancing energy efficiency and reducing carbon footprints.In conclusion, the Wall Panel Roll Forming Machine has brought a revolution to the construction industry. Its time-saving, cost-effective, and customizable features have made it the preferred choice for manufacturers and contractors worldwide. With its technological advancements and eco-friendly production practices, this machine paves the way for modern, energy-efficient, and sustainable buildings. Embrace the future of construction and invest in a Wall Panel Roll Forming Machine today!Keywords: Wall Panel Roll Forming Machine, China manufacturers, suppliers, factory, construction, efficiency, quality, game-changer, traditional methods, roll forming technology, production line, rollers, forming stations, cutting systems, raw materials, galvanized steel, aluminum coils, precise profiles, advantages, labor costs, material usage, customization, flexibility, safety, green construction practices, environmentally friendly materials, sustainable buildings.
Looking for a Quality Horizontal 3D Panel Machine at Factory Price? Check Out Top China Manufacturers Now!
article as follows:A breakthrough technology in the construction industry has taken the market by surprise. The Horizontal Barrel Vault Panel Manufacturing Machine has revolutionized the way buildings are made. With its innovative design and high-quality production, it has become the new standard for construction.The Horizontal Barrel Vault Panel Manufacturing Machine was created by industry experts to address the growing demand for more efficient and reliable building solutions. It produces a unique and durable product that significantly reduces construction time, labor, and cost. It is a game-changer in the construction industry that has been waiting for a new, more efficient way to build.The technology behind the Horizontal Barrel Vault Panel Manufacturing Machine is state-of-the-art, incorporating the latest in manufacturing technologies. It uses horizontal 3D panel technology, which results in panels that are extremely strong, rigid, and lightweight. This means that builders can construct taller, more extensive structures faster and with less cost.The Horizontal Barrel Vault Panel Manufacturing Machine was developed with a focus on energy efficiency, and environmental sustainability. It uses eco-friendly materials that are environmentally friendly, making it a go-to choice for architects and engineers. It has a low carbon footprint, uses less energy, and reduces waste, making it a cost-effective and sustainable solution.The machine’s use of horizontal 3D panels makes it more versatile and adaptable than traditional construction methods. The panels can be used to create long spans, and the machine can produce panels of various shapes and sizes. This flexibility opens up a whole new world of possibilities for architects and builders to create complex and visually appealing structures.The Horizontal Barrel Vault Panel Manufacturing Machine is user-friendly and efficient, with excellent automation features that reduce the likelihood of human error. It has an integrated control system that allows users to input specific measurements, produces the desired panels, and reduces waste. The intuitive interface makes it easy for beginners to operate, and the machine requires minimal maintenance.Several companies in China manufacture and supply the Horizontal Barrel Vault Panel Manufacturing Machine. The cost of the machine varies. However, buyers should expect a higher initial investment in exchange for long-term cost savings and faster construction. The suppliers offer after-sale services such as installation, training, and maintenance, ensuring a seamless switch to the new construction method.The Horizontal Barrel Vault Panel Manufacturing Machine has proved its value in several projects worldwide. It has been used in the construction of commercial buildings, residential homes, and industrial facilities. Its use reduces construction time by up to 50 percent, lowers labor costs, and produces more durable buildings that withstand earthquakes and natural disasters.In conclusion, the Horizontal Barrel Vault Panel Manufacturing Machine is the future of the construction industry. It offers innovative and sustainable solutions that make construction cheaper, faster, and safer. Its benefits are immense, and it’s only a matter of time before it becomes the norm in the construction industry. As the market becomes more competitive and demanding, the Horizontal Barrel Vault Panel Manufacturing Machine offers a significant edge, providing builders with the tools they need to build better, more sustainable, and efficient structures.
Innovative Technology Automates Tile Production for Increased Efficiency and Output
Title: Revolutionary Tiles Making Machine Transforms the IndustryIntroduction:In a ground-breaking development for the construction industry, a leading manufacturing company, renowned for its innovation, is set to unveil its latest creation - the Tiles Making Machine (TMM). Designed to revolutionize tile production, this state-of-the-art machinery is poised to streamline manufacturing processes and significantly enhance the efficiency and quality of tile production worldwide.Overview of the Tiles Making Machine (TMM):The Tiles Making Machine, developed by a team of expert engineers at a prominent manufacturing company, has been designed to meet the growing demands of the construction industry. This innovative machine integrates cutting-edge technology, automation, and advanced materials to craft tiles with unmatched precision and performance.Features and Benefits:The TMM boasts several remarkable features and benefits that set it apart from conventional tile manufacturing methods. Incorporating artificial intelligence and machine learning algorithms, this cutting-edge machine offers unparalleled accuracy, speed, and reliability. Its versatility allows for the creation of a wide range of tile designs, shapes, and sizes, ensuring a broad spectrum of options for customers.Moreover, the TMM reduces manual labor significantly, offering an automated solution for tile manufacturing. By minimizing human error and maximizing efficiency, this machine enables manufacturers to streamline their production processes, reducing costs and overall turnaround time. This transformative technology not only enhances the quality and consistency of tiles but also enhances worker safety by minimizing exposure to hazardous materials.Sustainability and Environmental Impact:Recognizing the need for sustainable practices within the construction industry, the Tiles Making Machine incorporates eco-friendly elements. By utilizing recycled materials and minimizing waste during the manufacturing process, the TMM aims to reduce the environmental impact of tile production. Furthermore, the machine operates on energy-efficient principles, ensuring a greener production process while reducing overall power consumption.Market Impact and Global Reach:The introduction of the Tiles Making Machine is expected to have a significant impact on the global tile manufacturing market. As the construction industry continues to grow, there is an increasing demand for efficient, cost-effective, and sustainable tile production. The TMM offers manufacturers the opportunity to enhance their productivity, competitiveness, and market presence.By enabling manufacturers to produce tiles of superior quality and diverse designs, the TMM will cater to a broader customer base, from individual homeowners to large-scale commercial projects. Its automation capabilities and streamlined production processes will allow manufacturers to meet deadlines, mitigate supply chain disruptions, and stay ahead in the highly competitive market.Conclusion:The Tiles Making Machine (TMM) has the potential to redefine tile manufacturing globally. By combining cutting-edge technology, automation, sustainability, and versatility, this revolutionary machine offers tile manufacturers an unparalleled advantage in terms of efficiency, productivity, and quality. With its ability to optimize production processes and reduce costs, the TMM is poised to transform the construction industry, meeting the demands of a rapidly growing market.As manufacturers adopt this state-of-the-art machinery, the TMM will pave the way for a new era in tile production, setting new standards of excellence. Additionally, its sustainable practices and eco-friendly manufacturing process will contribute to a greener construction industry, addressing environmental concerns. Underlining the commitment to innovation and progress, the Tiles Making Machine is set to leave an indelible mark on the future of tile manufacturing.
High Precision Cut To Length Line Metal Sheet Cutting Machine for Efficient Sheet Metal Slitting
and Sheet Metal Slitter Machine.When it comes to cutting metal sheets, it is imperative to have a reliable and precise Cut-To-Length Machine and Sheet Metal Slitter Machine. These machines are designed to offer efficient precision cutting of metal sheets, which is essential in most metal fabrication industries. The High Precision Cut-To-Length Line Metal Sheet Cutting Machine/Sheet Metal Slitter Machine is among the most sought after machines in the market today.This machine is made using high-quality materials that guarantee its durability and efficiency. The machine is specifically designed to cut metal sheets into specific sizes, lengths, and widths, making it ideal for various metal fabrication projects. It utilizes high precision sensors that measure and cut metal sheets according to the desired lengths.One of the benefits of this machine is its ability to deliver high precision cutting. The machine is designed to deliver accurate and consistent cuts that meet your specifications. This is essential in ensuring that the finished products meet the required standards, and there is no wastage of materials.The High Precision Cut-To-Length Line Metal Sheet Cutting Machine/Sheet Metal Slitter Machine is also versatile. It can be used to cut different types of metal sheets, including aluminum, galvanized, cold-rolled, and stainless steel. This makes it ideal for use in different industries such as construction, automotive, and aerospace.Another advantage of this machine is its efficiency. The machine is designed to operate at high speeds, enabling it to cut several metal sheets within a short period. This not only saves time but also increases production capacity, which is essential in meeting high demand in the market.In conclusion, the High Precision Cut-To-Length Line Metal Sheet Cutting Machine/Sheet Metal Slitter Machine is a vital investment for any metal fabricator. It offers high precision cutting, versatility, and efficiency, which are essential in meeting the demands of the market. If you are looking to enhance your metal fabrication business's productivity, then this machine is a must-have.
Innovative Profiling Equipment for Creating Glazed Tiles
Title: Advanced Profiling Equipment Revolutionizes Glazed Tile ManufacturingIntroduction:In a groundbreaking development that is set to transform the glazed tile manufacturing industry, a leading company has unveiled its latest innovation - advanced profiling equipment. This cutting-edge technology eliminates the need for manual profiling, streamlining the production process and ensuring unparalleled precision and efficiency. By leveraging this state-of-the-art machinery, manufacturers can now produce an exquisite range of glazed tiles in a faster, more cost-effective, and sustainable manner.Innovative Technology:The newly-introduced advanced profiling equipment is the result of extensive research and development by a renowned manufacturer. By fusing automation and computer-controlled precision machinery, this equipment allows for the shaping and profiling of glazed tiles in a highly accurate and efficient manner. With superior profiling capabilities, the equipment can achieve intricate designs and impeccable finishing, rendering each glazed tile a work of art.Enhanced Precision:The traditional method of manual profiling often resulted in inconsistencies in tile shape, leading to production delays and significant material wastage. However, with the advent of advanced profiling equipment, such concerns are now a thing of the past. The computerized controls and precise movements of the machinery ensure that each tile is uniform, with perfectly calibrated dimensions as specified by the manufacturer. This increased precision results in a seamless construction process and facilitates easy installation for end-users.Streamlined Production and Increased Efficiency:One of the primary advantages of the new profiling equipment is its ability to significantly boost production capacity while minimizing manufacturing time. The advanced technology automates various stages of the profiling process, including cutting and shaping, thereby reducing the reliance on manual labor. This not only speeds up the production cycle but also reduces costs associated with human errors and worker fatigue. Additionally, the machinery's efficiency ensures a higher output of glazed tiles, meeting market demands effectively.Sustainable Manufacturing:As the global focus on sustainable practices intensifies, the need for eco-friendly manufacturing processes has become more critical than ever. Advanced profiling equipment is a solution to this challenge. By minimizing resource wastage and optimizing the production process, this machinery dramatically reduces the carbon footprint of glazed tile manufacturing. Moreover, it promotes the use of recyclable materials, contributing to the overall sustainability of the industry.Durability and Longevity:The integration of advanced profiling equipment ensures that glazed tiles produced possess exceptional durability and longevity. The precision cutting and shaping techniques employed by the machinery create tiles that fit seamlessly and interlock securely. This eliminates the risks of cracks, breakages, or uneven installation, guaranteeing a reliable, long-lasting flooring or walling solution for customers across various sectors.Revolutionizing Tile Design:The advent of advanced profiling equipment has unlocked a new era of design possibilities for glazed tiles. Manufacturers can now experiment with intricate shapes, beveled edges, and unique aesthetics that were previously difficult to achieve through manual profiling. This has led to an explosion of creativity and innovation in the industry, with customers benefiting from an extensive range of designs and patterns to suit their individual preferences and requirements.Conclusion:The introduction of advanced profiling equipment marks a significant turning point in the glazed tile manufacturing industry. This cutting-edge machinery not only streamlines production processes but also ensures unparalleled precision, efficiency, sustainability, and durability. With limitless design possibilities, the application of this advanced technology promises to revolutionize the realm of glazed tiles, enhancing the quality of construction projects worldwide.
Reliable Sheet Metal Fabrication Services: Stainless Steel, Aluminum & Custom Metal
Title: Streamlining Your Business with Steel Sheet Making Machines: Unleashing the Power of Custom Metal FabricationIntroduction:In today's competitive market, businesses across various industries are increasingly turning to custom metal fabrication services to meet their unique manufacturing requirements. Among the many processes involved in metal fabrication, Steel Sheet Making Machines play a critical role in ensuring high-quality stainless steel and aluminum sheet production. This article aims to explore the significance of Steel Sheet Making Machines in the realm of custom metal fabrication and how they contribute to the manufacturing success of businesses across the globe.1. The Essence of Steel Sheet Making Machines:Steel Sheet Making Machines are advanced manufacturing tools designed to accurately shape and cut steel sheets into desired forms. These machines incorporate various components and mechanisms, including hydraulic systems, feeders, rollers, shears, and cutting devices. By utilizing cutting-edge technologies, these machines streamline the metal fabrication process, enhancing efficiency, precision, and overall productivity.2. Precision and Consistency:One significant advantage of Steel Sheet Making Machines is their ability to consistently produce high-quality steel sheets with utmost precision. The intricate mechanisms and cutting-edge technologies integrated into these machines ensure consistent sheet thickness, tight tolerances, smooth edges, and well-defined shapes. Custom metal fabrication companies can deliver products that meet or even exceed the expectations of their clients, reinforcing their reputation in the market.3. Increased Efficiency and Productivity:Steel Sheet Making Machines revolutionize the manufacturing process, significantly reducing production time and increasing efficiency. These machines can perform multiple operations, such as cutting, bending, and shaping, in a single run, eliminating the need for separate machinery or manual labor. The automated processes of these machines enable businesses to produce larger volumes of steel sheets with minimal human intervention, thereby increasing productivity and reducing labor costs.4. Versatility and Customization:Custom metal fabricators often deal with diverse client requirements, necessitating the ability to produce steel sheets in various shapes, sizes, and thicknesses. Steel Sheet Making Machines offer extensive flexibility and adaptability, allowing businesses to cater to these diverse demands. With adjustable settings and versatile tooling options, these machines can fabricate customized steel sheets to match unique specifications, enabling businesses to deliver tailored solutions to their customers.5. Cost and Resource Optimization:By investing in Steel Sheet Making Machines, businesses can optimize their use of resources and reduce costs in the long run. These machines minimize material wastage through precise cutting and shaping capabilities, ensuring minimal scrap and maximizing yield. Additionally, the automated nature of these machines reduces the reliance on manual labor, saving on labor expenses.Conclusion:In conclusion, Steel Sheet Making Machines have emerged as indispensable tools in the realm of custom metal fabrication. Their ability to deliver precision, consistency, efficiency, and customization has revolutionized the manufacturing industry. By investing in these advanced machines, businesses can streamline their metal fabrication processes, cater to diverse client requirements, minimize costs, and stay ahead in the competitive market. Whether it is stainless steel sheet metal fabrication, aluminum sheet metal fabrication, or any other custom metal fabrication needs, the utilization of Steel Sheet Making Machines ensures successful outcomes and drives the growth of businesses across the globe.Keywords: Steel Sheet Making Machine, custom metal fabrication, stainless steel sheet metal fabrication, aluminum sheet metal fabrication, metal fabrication services, precision manufacturing, increased productivity, cost optimization, versatile tooling options.
Easy-to-Use Hydraulic Multi-Outlet Forming Machine for Versatile Food Processing
Meat processing has come a long way over the years. Advances in technology and machinery have made it easier to process meat, as well as other foods. One such advancement is the development of forming machines, specifically the all hydraulic microprocessor controller, multi-outlet forming machine.With this advanced technology, processors are able to portion, shape, and form various types of meat, cheese, and even vegetables. The machine is designed to be easy to maneuver throughout the plant, allowing for seamless integration with other processing equipment.One of the benefits of the all hydraulic, microprocessor controller, multi-outlet forming machine is its versatility. Processors are able to utilize the machine to form a wide variety of meats, including beef, pork, poultry, fish, veal, lamb, as well as cheese and vegetables.The machine's microprocessor controller enables precise and accurate portion control, ensuring consistent product size and weight. This can be especially beneficial when it comes to packaging and labeling meat products for retail sales.Another key feature of the all hydraulic, microprocessor controller, multi-outlet forming machine is its flexibility. The machine can be outfitted with a wide range of forming plates, allowing processors to create a variety of shapes and sizes, from patties to nuggets. This is particularly useful for processors who are looking to create unique and innovative meat products.In addition to its versatility and flexibility, the all hydraulic, microprocessor controller, multi-outlet forming machine is also designed to be easy to clean and maintain. This is important for ensuring food safety and reducing the risk of foodborne illness.Overall, the all hydraulic, microprocessor controller, multi-outlet forming machine is a crucial piece of equipment for processors looking to streamline their operations and increase efficiency. Its ability to form a wide range of meats, cheese, and vegetables with precision and accuracy is unparalleled, making it a must-have for any modern meat processing facility.If you're in the market for a forming machine, be sure to consider the benefits of the all hydraulic, microprocessor controller, multi-outlet forming machine. With its versatility, flexibility, and ease of use, it's sure to take your processing capabilities to the next level.
Could the Universe be Devoured by a Black Hole-Creating Machine?
The prospect of the universe being swallowed up by a black hole is a nightmare scenario that few ever thought would become a reality. Yet, it appears that ominous possibility may have come a step closer to being realized after a mind-bogglingly complicated machine originally designed to create black holes was switched back on, now with double the power it had before. Scientists around the world are warning that this could have catastrophic consequences for our planet and indeed for the entire universe itself.The machine in question is a particle accelerator, called the Large Hadron Collider (LHC), that is based in Geneva, Switzerland. This giant machine is the most powerful particle accelerator ever built and has already produced a series of groundbreaking discoveries in particle physics. However, the machine is also highly controversial, as some scientists fear that it could create dangerous black holes that could potentially destroy the planet.The machine was first built in 2008 and was designed to recreate the conditions of the Big Bang. By smashing particles together at incredibly high speeds, scientists hoped to learn more about the building blocks of the universe. However, some scientists warned that the machine could create black holes so powerful that they could eventually destroy the planet and the entire universe.Despite these concerns, the machine was switched on for the first time in September 2008 and quickly produced a series of spectacular results. However, after just nine days of running, the machine broke down and had to be shut down for repairs. Over the next few years, the machine was slowly brought back up to speed, but many scientists remained wary of its potential to create black holes.Now, it seems that those concerns may have been justified. According to reports, the machine has been switched back on at double its previous power, and there are fears that it could now create black holes that are much more powerful than before. Scientists warn that if one of these black holes were to escape into the wider universe, it could quickly grow in size and eventually swallow up everything in its path, including stars, planets, and even entire galaxies.The consequences of such an event would be catastrophic. If the universe were destroyed, it would mean the end of everything we know and love. It would also mean the end of life itself, as we know it. This is why so many scientists have warned against the potential dangers of the LHC and other particle accelerators.One of the main problems with the LHC is that it operates at such high energies that it is impossible to fully predict what will happen when particles collide. This means that there is always a risk that the machine could create something that could be catastrophic for the entire universe.Despite these concerns, many scientists have argued that the risks are minimal and that the benefits of the LHC far outweigh any potential dangers. They argue that the machine has already produced a wealth of valuable scientific data and that it could lead to groundbreaking new discoveries in the field of particle physics.However, others remain more cautious. They argue that we simply do not know enough about the workings of the universe to predict what will happen if we continue to push the limits of particle physics. They warn that the LHC could be a ticking time bomb that could destroy everything we hold dear.For now, the LHC continues to operate at double its previous power, and scientists around the world will be watching nervously to see what happens next. If the machine does create a black hole that is powerful enough to destroy the universe, it could be a wake-up call for us all about the dangers of meddling with the fundamental building blocks of the universe.In conclusion, the potential for the LHC to create a black hole that could destroy the entire universe is a prospect that is both awe-inspiring and terrifying in equal measure. While many scientists argue that the benefits of the machine far outweigh any potential risks, others remain more cautious and warn that we simply do not know enough about the universe to predict what will happen if we continue to push the limits of particle physics. The future of the LHC remains uncertain, but one thing is for sure: the consequences of its actions could be catastrophic.