High-Quality Light Gauge Steel Roll Forming Machine for Sale
By:Admin
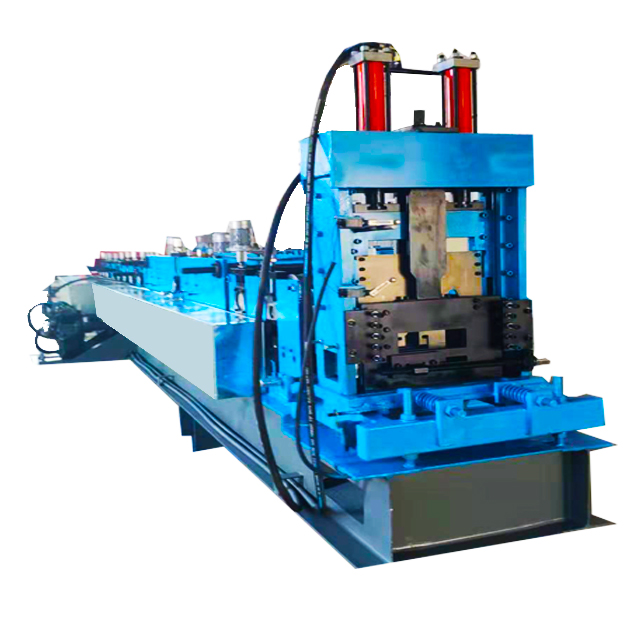
In recent years, the construction industry has seen a significant shift towards using light gauge steel (LGS) as a primary building material. This is due to the numerous advantages that LGS offers, including its strength, durability, and sustainability. With the increasing demand for LGS construction, the need for efficient and reliable manufacturing equipment has become more critical than ever.
Recognizing this demand, {Company Name} has introduced a state-of-the-art Light Gauge Steel Roll Forming Machine that is set to revolutionize the construction industry. This cutting-edge machine is designed to streamline the process of manufacturing LGS components, making it faster, more cost-effective, and more precise than ever before.
The Light Gauge Steel Roll Forming Machine from {Company Name} is equipped with the latest technological innovations, including advanced computerized controls, precision tooling, and high-speed production capabilities. This allows for the rapid and seamless production of LGS components, such as studs, tracks, joists, and panels, with unparalleled accuracy and consistency.
One of the key features of the Light Gauge Steel Roll Forming Machine is its versatility. It can be easily customized to accommodate a wide range of LGS profiles and sizes, making it suitable for a variety of construction projects, from residential homes to commercial buildings. This flexibility ensures that the machine can meet the diverse needs of architects, engineers, and construction professionals.
Furthermore, {Company Name} takes pride in its commitment to sustainability and environmental responsibility. The Light Gauge Steel Roll Forming Machine is designed to minimize material waste and energy consumption, while maximizing the efficiency of the manufacturing process. This not only benefits the bottom line of construction companies but also contributes to a greener and more sustainable construction industry.
The introduction of the Light Gauge Steel Roll Forming Machine from {Company Name} comes at a time when the construction industry is experiencing a growing demand for LGS construction. With its advanced technology and superior performance, this machine is poised to meet this demand and set a new standard for the manufacturing of LGS components.
In addition to its cutting-edge technology, {Company Name} stands out for its commitment to customer satisfaction and support. The company offers comprehensive training and technical assistance to ensure that customers can maximize the potential of the Light Gauge Steel Roll Forming Machine and achieve optimal results in their manufacturing process.
With the introduction of the Light Gauge Steel Roll Forming Machine, {Company Name} is positioned as a leader in the manufacturing and supply of equipment for the LGS construction industry. The company's dedication to innovation, quality, and customer service sets it apart as a trusted partner for construction companies looking to embrace the benefits of LGS construction.
In conclusion, the Light Gauge Steel Roll Forming Machine from {Company Name} represents a significant advancement in the manufacturing of LGS components. Its advanced technology, versatility, and commitment to sustainability make it a game-changer for the construction industry. As the demand for LGS construction continues to grow, {Company Name} is well-positioned to lead the way with its innovative and reliable manufacturing equipment.
Company News & Blog
Shop for Quality Roofing Sheet Manufacturing Machines on Sale from Chinese Suppliers
Title: Evolutionary Advancements in Roofing Sheet Manufacturing Machines Lead to Increased DemandIntroduction:In recent years, the roofing industry has witnessed a rapid surge in demand for durable and efficient roofing sheets. This demand has been met by cutting-edge technology and innovations in roofing sheet manufacturing machines. With an increasing number of manufacturers entering the market, the industry has become highly competitive. Today, we explore the significant developments in this sector, highlighting the role of advanced roofing sheet manufacturing machines in meeting customer requirements.Section 1: Evolution of Roofing Sheet Manufacturing MachinesRoofing sheet manufacturing machines have evolved significantly, offering improved efficiency, precision, and versatility in sheet production. Initially, these machines were manual and required skilled operators. However, with the advent of technology, automated machines have emerged, resulting in enhanced productivity and reduced labor costs. These modern machines utilize computer numerical control (CNC) technology to achieve higher accuracy and consistency in manufacturing processes.Section 2: Innovative Features of Contemporary Roofing Sheet Manufacturing MachinesContemporary roofing sheet manufacturing machines boast a range of innovative features that contribute to the high quality of the final product. These include:1. Material Compatibility: Modern machines accommodate various roofing materials such as galvanized steel, aluminum, and polycarbonate. This flexibility allows manufacturers to cater to diverse customer needs and expand their product offerings.2. Customization Capabilities: The ability to customize sheet dimensions, profiles, and surface patterns enables manufacturers to produce roofing sheets tailored to specific project requirements. This has significantly contributed to the growing popularity of these machines in the construction industry.3. High-Speed Manufacturing: Advanced roofing sheet manufacturing machines can produce large quantities of sheets within a short period, catering to the increasing demand for faster turnaround times in the industry.4. Energy Efficiency: With a focus on sustainability, many roofing sheet manufacturing machines are designed to minimize energy consumption. These machines utilize intelligent controls and power-saving mechanisms to optimize efficiency while reducing environmental impact.Section 3: Benefits of Investing in Modern Roofing Sheet Manufacturing MachinesThe adoption of these technologically advanced machines has proven to be beneficial for manufacturers in various ways. Some key advantages include:1. Cost Reduction: Automation and increased production efficiency result in reduced labor costs and waste, increasing profitability for manufacturers. Additionally, the versatility to work with different materials minimizes setup and changeover times, contributing to cost savings.2. Improved Quality Control: Automated processes ensure consistent quality and dimensional accuracy in each sheet produced. This not only enhances customer satisfaction but also reduces the likelihood of product recalls and associated costs.3. Enhanced Safety: Modern machines prioritize operator safety with built-in safety features and improved control systems, reducing the risks associated with manual labor.4. Competitive Edge: Manufacturers employing advanced roofing sheet manufacturing machines gain a significant competitive advantage in terms of offering superior products with shorter lead times as compared to their counterparts who rely on traditional manufacturing methods.Conclusion:The evolution and advancements in roofing sheet manufacturing machines have revolutionized the roofing industry, enabling manufacturers to meet the rising demand for durable and customizable roofing solutions. With the ability to produce high-quality roofing sheets efficiently, manufacturers are set to capitalize on the growing market opportunities. As technology continues to advance, the industry can expect even more innovative solutions that cater to the changing needs of the construction sector.
High-Quality Roll Forming Machine for Wall Panel Production
The Wall Panel Roll Forming Machine is a cutting-edge piece of equipment designed to revolutionize the production of wall panels. This innovative machine, which is manufactured by a company specializing in roll forming machinery, has been hailed as a game-changer in the industry due to its advanced technology and impressive capabilities.The Wall Panel Roll Forming Machine features state-of-the-art engineering, precision manufacturing, and high-quality components. Its cutting-edge design allows for the rapid and efficient production of wall panels, making it an ideal choice for companies looking to improve their manufacturing processes and increase their productivity.One of the key features of the Wall Panel Roll Forming Machine is its versatility. It is capable of producing a wide range of wall panel designs, including standard panels, insulated panels, and decorative panels. This flexibility makes it suitable for a variety of applications, from residential construction to commercial and industrial projects.In addition to its flexibility, the Wall Panel Roll Forming Machine is also known for its high-speed production capabilities. Thanks to its advanced technology and precision engineering, this machine is able to produce wall panels at an impressive rate, significantly reducing production time and costs for manufacturers.Furthermore, the Wall Panel Roll Forming Machine is designed with user-friendly features, making it easy to operate and maintain. This user-friendly design ensures that operators can quickly and efficiently set up the machine for production, minimizing downtime and maximizing productivity.The company behind the Wall Panel Roll Forming Machine is renowned for its expertise in roll forming machinery. With a strong focus on research and development, the company has consistently pushed the boundaries of innovation in the industry, leading to the creation of cutting-edge machines like the Wall Panel Roll Forming Machine.In addition to its commitment to innovation, the company also places a strong emphasis on quality and reliability. Each machine is built to the highest standards, using top-grade materials and advanced manufacturing processes to ensure that it meets the strictest performance and durability requirements.Moreover, the company has an impressive track record of delivering exceptional customer service and support. From the initial consultation to installation and ongoing maintenance, the company provides comprehensive assistance to its customers, ensuring that they are fully satisfied with their investment in the Wall Panel Roll Forming Machine.The Wall Panel Roll Forming Machine is set to have a significant impact on the wall panel manufacturing industry, offering manufacturers a highly efficient and versatile solution for their production needs. With its advanced technology, high-speed production capabilities, and user-friendly design, this machine is poised to become a key asset for companies looking to improve their manufacturing processes and stay ahead of the competition.In conclusion, the Wall Panel Roll Forming Machine is a groundbreaking piece of equipment that is set to transform the way wall panels are produced. With its advanced technology, high-speed production capabilities, and user-friendly design, it offers manufacturers an efficient and versatile solution for their production needs. Combined with the company's dedication to innovation, quality, and customer service, the Wall Panel Roll Forming Machine is undoubtedly a game-changer in the industry.
How to Build a Sheet Metal Barn in 6 Easy Steps: A Step-by-Step Guide
article.If you’re looking for a sturdy and durable structure to protect your property or livestock from the elements, then building a sheet metal barn may be the solution for you. Sheet metal barns are a cost-effective and easy-to-build option that offers a long-lasting shelter for your animals, equipment, and machinery. In this article, we provide you with six easy steps to build your own sheet metal barn.Step 1: Plan Your BarnThe first step in building your sheet metal barn is to gather all the necessary information. This includes determining the size of the barn you need, choosing the right location, getting appropriate permits and approvals, and creating a detailed plan. A full-scale model and an accurate blueprint will help you to visualize the structure, avoid costly errors, and ensure that your barn meets local building codes and regulations.Step 2: Pour Your FoundationWith your plan in hand, the next step is to pour a solid foundation for your sheet metal barn. Concrete is the most common material used for this purpose, but you can also use wood posts or piers. The foundation must be durable and strong enough to support the weight of the structure and withstand harsh weather conditions.Step 3: Erect Your FrameOnce the foundation is in place and has had time to cure, the next step is to erect the frame of your sheet metal barn. Wood or steel posts are the most popular materials for frames, but you can also use other materials, such as concrete. The frame should be level and square to ensure that the sheet metal panels fit perfectly and the barn is structurally sound.Step 4: Install Your Roof and WallsWith the frame completed, the next step is to install the roof and walls of your sheet metal barn. Galvanized sheet metal is a popular option due to its durability, strength, and resistance to rust and corrosion. You can also use other materials, such as polycarbonate panels, to add natural light and ventilation. Sheet metal panels should be installed securely, with appropriate screws and anchors, to prevent water leakage and damage.Step 5: Add Your Doors and WindowsTo complete your sheet metal barn, add doors and windows as needed. Large doors for machinery and smaller doors for livestock are essential, and windows can provide natural light and ventilation. Make sure that doors and windows are appropriately secured and protected from the elements to ensure the safety of your animals and equipment.Step 6: Finishing TouchesFinally, add any finishing touches, such as insulation, ventilation, and gutters, to your sheet metal barn. These features will help to improve the comfort and safety of your animals and equipment, and protect your barn from water damage.ConclusionBuilding a sheet metal barn may seem daunting, but by following these six easy steps, you can create a durable and functional structure that meets your needs and budget. With careful planning, appropriate materials, and attention to detail, your sheet metal barn will provide you with years of protection and peace of mind.
Quality Cold Roll Forming Machines, Roof Panel & Tile Forming Machines, and More - Xiamen HF Roll Machinery
Title: Enhancing Efficiency and Quality with Corrugated Roof Panel Forming EquipmentIntroduction:In the rapidly evolving field of construction, technological advancements have revolutionized traditional methods, enhancing efficiency and quality. One such innovation is the corrugated roof panel forming equipment, a versatile machine that facilitates the production of high-quality corrugated roof panels. Xiamen HF Roll Machinery Co., Ltd. specializes in manufacturing top-notch cold roll forming machines, including the highly efficient corrugated roof panel forming equipment. In this blog, we will explore the functionalities and benefits of this equipment, highlighting its role in modern construction practices.1. Understanding Corrugated Roof Panel Forming Equipment:Corrugated roof panel forming equipment is a specialized machine designed for the precise production of corrugated roof panels. Engineered with advanced roll-forming technology, this equipment streamlines the manufacturing process, delivering consistently excellent results. It employs a cold roll forming process, ensuring optimal strength and durability of the final product.2. Features and Capabilities:The corrugated roof panel forming equipment offered by Xiamen HF Roll Machinery Co., Ltd. boasts several notable features that set it apart from its counterparts. These include:a. Versatility: This equipment supports the production of various corrugated roof panel designs, allowing customization according to client requirements.b. High-speed Production: Advanced motor control systems enable high-speed production of roof panels, optimizing manufacturing efficiency.c. Precise Panel Dimensions: Computer-controlled settings guarantee precise panel dimensions, ensuring uniformity and accuracy in every unit manufactured.d. Durability and Quality: The equipment operates with precision-engineered components, resulting in superior durability and high-quality outputs.e. User-friendly Interface: The machine is equipped with an intuitive operator interface that enables easy configuration, adjustments, and monitoring during the manufacturing process.3. Advantages of Corrugated Roof Panel Forming Equipment:Implementing corrugated roof panel forming equipment offers numerous benefits in the construction industry:a. Enhanced Efficiency: The speed and accuracy of panel production significantly reduce labor costs and project timelines. This leads to improved project management and increased profitability.b. Superior Quality: The use of precision engineering techniques ensures panels with exceptional dimensional accuracy and uniformity, minimizing errors and maximizing structural integrity.c. Design Flexibility: The equipment supports diverse panel designs, allowing for customization and meeting specific architectural requirements. This enables versatility in construction projects.d. Cost Savings: In addition to reduced labor costs, the durable and low-maintenance equipment minimizes long-term expenses, optimizing overall project budgets.e. Environmental Sustainability: The cold roll forming process utilizes energy-efficient technology, reducing energy consumption and minimizing carbon footprint.4. Application Areas:Corrugated roof panels find extensive application in various construction projects, including:a. Residential Roofing: The durability, weather resistance, and aesthetic appeal of these panels make them an ideal choice for residential roofing solutions.b. Commercial Buildings: The versatility of corrugated roof panels makes them suitable for large-scale commercial and industrial buildings, providing robust roofing solutions.c. Agricultural Structures: The lightweight nature and excellent durability of these panels make them perfect for agricultural structures like barns and warehouses.d. Temporary Structures: Corrugated roof panels are frequently used in temporary structures such as event pavilions, carports, and storage sheds.Conclusion:Corrugated roof panel forming equipment has revolutionized the construction industry by improving efficiency, reducing costs, and enhancing quality. Offering an array of benefits, including versatility, high-speed production, precise dimensions, and durability, this equipment has become indispensable in modern construction practices. With Xiamen HF Roll Machinery Co., Ltd. offering top-of-the-line equipment, such as the corrugated roof panel forming machine, construction companies can ensure exceptional results, meeting both functional and aesthetic requirements. Invest in this advanced technology to boost the overall efficiency, quality, and profitability of your construction projects.
Increase Production Efficiency and Prevent Film Cracking with Advanced Web Tension Control Systems for Slitting Machines
The Slitting and Cutting Machine: An OverviewWhen it comes to manufacturing materials such as paper, plastic film, or even textiles, the slitting and cutting machine is an essential piece of equipment. These machines are designed to take large rolls of material and cut them down into the desired size and shape, allowing for easier handling and processing.One of the most important aspects of a slitting and cutting machine is its ability to maintain proper tension throughout the process. This is where web tension control systems come into play. These systems help prevent film cracking and other issues that can arise when the tension is not properly controlled.There are several different types of slitting and cutting machines available on the market today. Some are designed for specific materials such as paper or plastic film, while others are more versatile and can handle a variety of materials.One common type of slitting and cutting machine is the rotary shear. This machine uses a set of sharp blades that rotate against a stationary blade, effectively cutting the material as it passes through. The blades can be adjusted to vary the width of the cut, allowing for greater flexibility in production.Another type of slitting and cutting machine is the crush cutter. This machine uses a roller with a dull blade that crushes the material against a stationary blade, effectively cutting it in the desired width. Crush cutters are often used for materials that are more delicate or easily damaged.Regardless of the type of slitting and cutting machine being used, proper maintenance is essential to ensure optimal performance and longevity. Routine inspections and cleaning can help prevent issues from arising, while regular calibration can help ensure that the machine is cutting accurately and efficiently.In conclusion, the slitting and cutting machine is a vital piece of equipment in many manufacturing industries. With the right equipment and maintenance, it can help increase efficiency, reduce waste, and improve the overall quality of the finished product. Ensure to also incorporate web tension control systems to prevent film cracking and other similar issues.
Steel Roofing Tile Roll Forming Machine: A Durable Roofing Solution
Glazed Steel Roofing Tile Roll Former Now AvailableFor those in the construction industry, the demand for continuous, efficient, and high-quality production is essential. To meet the industry’s needs, we are excited to announce the release of our new Glazed Steel Roofing Tile Roll Former. Designed to streamline the manufacturing process, our Glazed Steel Roofing Tile Roll Former is the perfect addition to any construction site. Constructed with precision and care, our Roll Former is capable of producing quality steel roofing tiles with ease, making it the perfect solution for all your roofing needs. Our Glazed Steel Roofing Tile Roll Former is manufactured with state-of-the-art technology to ensure accuracy and speed. The machine is easy to use, and it saves valuable manufacturing time. It is suitable for producing a variety of roofing tiles, including trapezoidal sheet tiles, glazed tiles, corrugated tiles, and more. The machine's ability to produce tiles at high speeds ensures you can meet your production requirements.The Glazed Steel Roofing Tile Roll Former is designed with user-friendliness in mind. It is easy to install, operate, and maintain. It also comes with advanced safety features to ensure the safety of the operator and the machine. Our product is manufactured from high-quality materials, ensuring that it is durable and long-lasting. Its rugged construction allows for operation in harsh environments, making it ideal for use in various locations.At our company, we prioritize customer satisfaction, which is why we offer a 24/7 customer support team to address any queries or concerns about the product. Additionally, we provide a warranty to protect our customers and to assure them of the product's quality.In summary, our Glazed Steel Roofing Tile Roll Former is a game-changer in the construction industry. Its efficient production and user-friendly design make it the perfect solution for manufacturers looking to streamline their production process. Its durability and advanced safety features ensure a long-lasting investment that will prove to be valuable to your business.For more information about our Glazed Steel Roofing Tile Roll Former, visit our website or contact us today. We look forward to hearing from you soon!
How to Choose a Standing Seam Roof Panel Machine for Your Business
Title: Advanced Standing Seam Roof Panel Machine Revolutionizing Roofing IndustryIntroduction:With the constant need for efficient and innovative solutions in the roofing industry, the introduction of an advanced Standing Seam Roof Panel Machine (name omitted) is set to revolutionize the way roofs are manufactured and installed. Developed by a reputable company known for their dedication to quality and precision engineering, this state-of-the-art machine promises to streamline the roofing process while offering enhanced durability and sustainability. Let's delve into the features and benefits of this cutting-edge technology.1. Efficiency and Precision:The Standing Seam Roof Panel Machine combines years of experience with advanced engineering to deliver a machine that is highly efficient and accurate in its operations. The machine is equipped with an automated control system, allowing for precise and consistent panel measurements, ensuring a perfect fit with minimal waste. With the ability to produce up to 60 feet of roof panel per minute, this innovative technology significantly reduces production time, increasing overall efficiency and productivity.2. Durability and Sustainability:In line with the company's commitment to environmentally friendly practices, the Standing Seam Roof Panel Machine employs sustainable materials and construction methods to produce highly durable roofing panels. The machine's design incorporates high-strength steel and state-of-the-art coatings to ensure resistance against harsh weather conditions, corrosion, and UV radiation. These panels offer exceptional longevity, reducing the need for frequent repairs or replacements, ultimately resulting in cost savings for both homeowners and commercial builders.3. Versatility and Customization:One of the standout features of the Standing Seam Roof Panel Machine is its ability to produce a wide range of panel profiles, allowing for extensive customization options. Clients can choose from a variety of panel widths, seam heights, and surface finishes, catering to their specific architectural requirements and aesthetic preferences. This versatility enables architects and designers to create unique roofing designs that harmonize with the overall style of the structure. Additionally, the machine's versatility ensures compatibility with various installation methods, making it suitable for both residential and commercial applications.4. Safety and Ease of Use:The Standing Seam Roof Panel Machine prioritizes operator safety and ease of use. The machine is equipped with advanced safety features, including emergency stop buttons, safety light curtains, and interlocking systems, ensuring a high level of protection during operation. Additionally, it boasts a user-friendly interface, allowing operators to navigate through different settings and controls with ease. The machine's ergonomic design and intuitive controls enable seamless operation, reducing the risk of errors and accidents.5. Training and Technical Support:Recognizing the importance of proper training and continuous technical support, the company offers comprehensive training programs to ensure operators have the necessary skills to operate the Standing Seam Roof Panel Machine effectively. The training covers machine operation, maintenance, troubleshooting, and safety protocols. Additionally, the company provides ongoing technical support to address any queries or concerns raised by customers, further enhancing the overall user experience.Conclusion:The introduction of the Standing Seam Roof Panel Machine marks a significant leap forward in the roofing industry, revolutionizing the way roofs are manufactured and installed. Its exceptional efficiency, precision, versatility, and sustainability make it a game-changer for architects, builders, and homeowners alike. With an unwavering commitment to quality and customer satisfaction, the company behind this advanced technology continues to innovate, ensuring the continuous improvement and development of the roofing industry.
Durable and Efficient Double Deck Roll Forming Machine for High-Volume Production
The Double Deck Roll Forming Machine has recently gained popularity in the metal forming industry, and {} is at the forefront of this innovative technology. This advanced machine has the capability to produce double-layered metal sheets, which offers significant advantages in terms of cost efficiency and production speed.With a focus on providing high-quality roll forming solutions to meet the evolving needs of the industry, {} has been a key player in the development and deployment of the Double Deck Roll Forming Machine. This state-of-the-art equipment is designed to increase productivity and optimize the production process, making it an essential part of modern metal forming operations.One of the key features of the Double Deck Roll Forming Machine is its ability to produce two different profiles simultaneously. This capability enables manufacturers to achieve greater flexibility in their production processes, as well as the ability to meet diverse customer requirements. With this machine, {} has empowered its clients to deliver a wide range of customized metal products, while also improving their overall production efficiency.In addition to its dual-profile capability, the Double Deck Roll Forming Machine also offers enhanced efficiency through its advanced control system. With precise control over the forming process, this machine ensures consistent quality and accuracy in the production of metal sheets. This level of control not only enhances the overall product quality but also minimizes material waste, ultimately leading to cost savings for manufacturers.Moreover, the Double Deck Roll Forming Machine is designed with a modular configuration, allowing for easy customization to suit specific production needs. This flexibility has been a game-changer for many manufacturers, as it enables them to adapt their production lines to accommodate various design requirements and material specifications. As a result, {} has empowered its clients to expand their product offerings and capture new business opportunities in the competitive metal forming market.Furthermore, {} has positioned itself as a leading provider of turnkey solutions for the roll forming industry, offering comprehensive support and expertise in the implementation of the Double Deck Roll Forming Machine. From initial consultation to installation and training, the company is committed to ensuring that its clients fully maximize the potential of this cutting-edge technology. This customer-centric approach has earned {} a reputation for reliability and excellence in the industry.Looking ahead, {} continues to innovate and develop new technologies to further advance the roll forming industry. With a strong focus on research and development, the company is dedicated to staying ahead of market trends and delivering innovative solutions that meet the evolving needs of manufacturers. As the demand for efficient, high-quality metal forming equipment continues to grow, {} remains committed to providing state-of-the-art solutions that drive success for its clients.In conclusion, the Double Deck Roll Forming Machine is a game-changing technology that has revolutionized the metal forming industry, and {} is at the forefront of this innovation. Through its commitment to excellence and customer satisfaction, the company has cemented its position as a trusted partner for manufacturers seeking to optimize their production processes and achieve new levels of efficiency and productivity. As the industry evolves, {} will continue to lead the way in delivering advanced roll forming solutions that empower manufacturers to thrive in the competitive market.
High Speed Metal Roof Panel Roll Forming Machine with Hydraulic Control System: Quality Supplier from China
Jiangyin Dingbo Technology CO., Ltd., a leading provider of roofing panel roll forming machines, has recently introduced their latest innovation - a high speed metal roof panel roll forming machine with hydraulic control system. This advanced machine is designed to efficiently produce metal roof panels with precision and speed, offering superior quality and performance.The 380V 50Hz high speed metal roof panel roll forming machine is equipped with a hydraulic control system, which ensures smooth and accurate operation. The hydraulic control system not only enhances the efficiency of the roll forming process but also enables precise control over the shaping and cutting of the metal sheets. This results in high-quality roof panel production that meets the stringent industry standards.One of the key features of this machine is its ability to produce metal roof panels in various sizes and profiles. The roll forming process involves feeding the metal sheets into the machine, where they are gradually shaped and cut into the desired profile. With the hydraulic control system, the machine can easily adjust its settings to accommodate different panel sizes and profiles, making it highly versatile and adaptable to the specific needs of the customers.Another notable feature of this machine is its high-speed production capability. With its efficient hydraulic control system and advanced technology, the roll forming process is significantly accelerated, allowing for faster production rates. This is especially beneficial for large-scale roofing projects where time is of the essence. The high-speed production not only increases efficiency but also reduces labor costs and enhances overall productivity.In addition to its impressive speed, this metal roof panel roll forming machine also ensures uncompromised quality. The advanced hydraulic control system ensures precise shaping and cutting, resulting in panels with smooth edges, consistent dimensions, and superior finish. The machine is designed to operate with utmost precision and accuracy, eliminating any potential errors or imperfections in the production process. This ensures that the produced roof panels meet the highest quality standards, providing customers with durable and aesthetically pleasing roofing solutions.Furthermore, Jiangyin Dingbo Technology CO., Ltd. emphasizes their commitment to customer satisfaction and reliability. As a reputable supplier of roof panel roll forming machines, the company strives to deliver top-notch products that meet and exceed customer expectations. They offer full support and assistance throughout the entire purchasing process, from consultation and customization to installation and after-sales service.Jiangyin Dingbo Technology CO., Ltd. continues to innovate and enhance their products to meet the evolving needs of the roofing industry. Their high-speed metal roof panel roll forming machine with hydraulic control system is a testament to their dedication to providing cutting-edge solutions that optimize efficiency, productivity, and quality. With this advanced machine, customers can benefit from faster production rates, superior panel quality, and enhanced overall performance.In conclusion, the introduction of the 380V 50Hz high speed metal roof panel roll forming machine with hydraulic control system by Jiangyin Dingbo Technology CO., Ltd. showcases their commitment to technological innovation and customer satisfaction. This advanced machine offers versatility, speed, and unmatched quality in the production of metal roof panels. As a trusted supplier, this company continues to revolutionize the roofing industry with their state-of-the-art solutions that enhance productivity and deliver excellence.
Top Aluminium Profile Bending Machine: Boost Efficiency and Precision
[Company Introduction]With a commitment to innovation and excellence, our company has been a leading manufacturer and supplier of industrial machinery for over two decades. Established in [year], we have consistently delivered top-notch products to various industries worldwide. Our cutting-edge technology, state-of-the-art manufacturing facilities, and a team of experienced professionals enable us to provide reliable and efficient solutions that cater to the diverse needs of our clients.[News Content]Aluminium Profile Bending Machine Sets New Industry Standards[City, Date] - Our company, a global leader in industrial machinery, has recently introduced its latest innovation, the Aluminium Profile Bending Machine. This remarkable machine sets new industry standards by offering precision and efficiency in bending aluminum profiles, revolutionizing the way aluminum fabrication is done.The Aluminium Profile Bending Machine is designed to meet the specific requirements of aluminum profile bending, ensuring accurate and consistent results. Its advanced features and cutting-edge technology make it the ideal choice for industries involved in aluminum fabrication, such as construction, automotive, aerospace, and furniture.Key Features of the Aluminium Profile Bending Machine include:1. Precision Bending: The machine's automated bending process ensures precise and uniform bending of aluminum profiles, eliminating variations and inconsistencies. It offers adjustable bending angles and radius options, allowing for versatile applications and meeting customized specifications.2. High Efficiency: The Aluminium Profile Bending Machine is equipped with a powerful motor and advanced hydraulic system, enabling high-speed and efficient bending operations. It reduces production time and increases overall productivity, leading to substantial cost savings for businesses.3. User-Friendly Interface: The machine is designed with an intuitive and user-friendly interface, making it easy to operate and control. The interface provides various programmable options, allowing operators to store and recall bending profiles quickly. It also features a comprehensive display that provides real-time information on bending processes, ensuring optimum control and monitoring.4. Durability and Reliability: Crafted from high-quality materials and components, the Aluminium Profile Bending Machine is built to last. It undergoes rigorous testing and quality checks to ensure its durability and reliability in demanding industrial environments. This ensures minimum downtime and maintenance costs, providing businesses with a reliable and long-lasting solution.5. Safety Features: Our priority is the safety of operators and the workplace. The Aluminium Profile Bending Machine is equipped with advanced safety features, including emergency stop buttons, safety sensors, and protective guards. These features significantly reduce the risk of accidents and injuries, ensuring a safe working environment.The introduction of the Aluminium Profile Bending Machine marks a significant milestone in our commitment to innovation and providing advanced solutions to our customers. The machine's diverse applications and unmatched precision make it an invaluable asset for industries reliant on aluminum fabrication.We are proud to contribute to the growth and success of our clients worldwide, as they can now enhance their production capabilities and deliver high-quality products with speed and efficiency.For more information about our Aluminium Profile Bending Machine and other industrial machinery, please visit our website or contact our sales team.[Company Name] is dedicated to continuous improvement and remains at the forefront of technological advancements, meeting the ever-evolving needs of the industry. With the Aluminium Profile Bending Machine, we further solidify our position as a trusted partner for industries seeking cutting-edge solutions for their manufacturing processes.