Roll Forming Machine for Deck Floors: Enhancing Efficiency and Precision
By:Admin
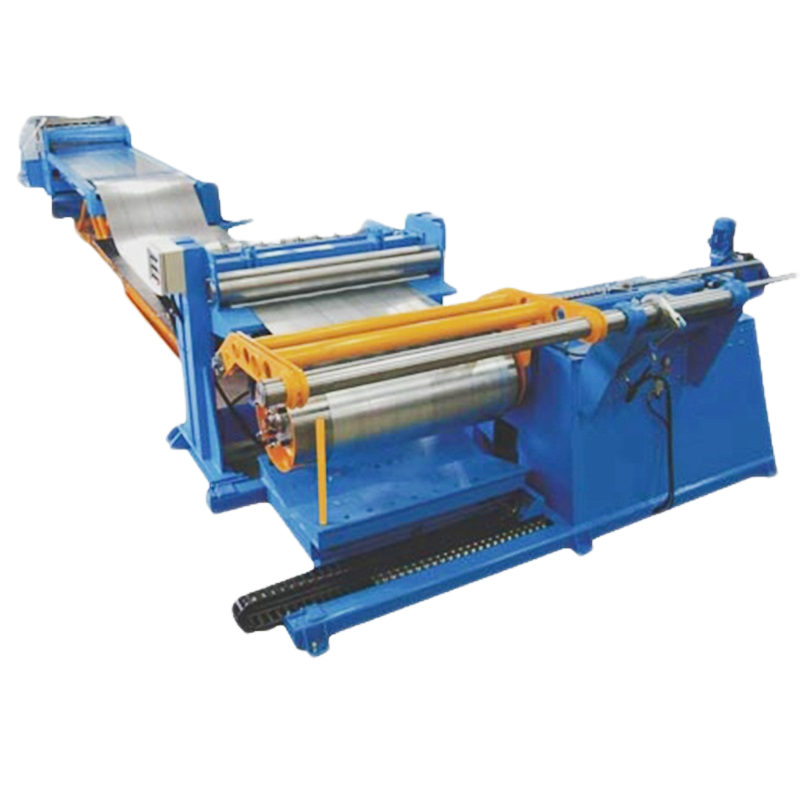
With a strong reputation for excellence in the manufacturing industry, our company has been a leading provider of innovative machinery and equipment for the construction sector for over two decades. We are dedicated to continuously improving our products and services to meet the ever-evolving needs of our customers. Our commitment to quality and customer satisfaction has propelled us to the forefront of the industry.
[News Content]
In the realm of construction machinery, one particularly noteworthy addition to our product lineup is the highly efficient Deck Floor Roll Forming Machine. Designed to revolutionize the process of creating durable and reliable deck floors, this advanced equipment offers unprecedented precision and speed.
The Deck Floor Roll Forming Machine effectively eliminates the traditional method of manually constructing deck floors, saving both time and labor costs. With its automated capabilities, it can swiftly and accurately produce high-quality deck floors that meet the stringent requirements of modern construction projects. The machine's cutting-edge technology ensures consistency and durability in every finished product.
One of the key features of this machine is its versatility. It can produce a wide range of deck floor profiles, catering to the diverse needs of different construction projects. Whether it is a simple residential deck or a complex commercial structure, the machine can adapt to the specific requirements with ease. This flexibility makes it an ideal choice for construction companies of all sizes.
Safety is paramount in any construction project, and the Deck Floor Roll Forming Machine prioritizes this aspect as well. The machine is equipped with the latest safety features, including emergency stop buttons, safety guards, and sensors to detect any potential malfunctions. This ensures a secure working environment for operators, minimizing the risk of accidents and injuries.
To enhance productivity, the machine has been meticulously designed for ease of operation. Its user-friendly interface allows operators to quickly understand and control the various parameters of the roll forming process. Additionally, the machine's automated functions reduce the need for constant monitoring, allowing operators to focus on other essential aspects of the project.
Moreover, the Deck Floor Roll Forming Machine is built to withstand the rigors of continuous operation. Its robust construction and high-grade materials ensure longevity and reliability, reducing downtime and maintenance costs. As a result, construction companies can seamlessly integrate this machine into their workflow, improving overall efficiency and profitability.
As sustainability becomes an increasingly important consideration in the construction industry, the Deck Floor Roll Forming Machine aligns with eco-conscious practices. By significantly reducing material waste and minimizing energy consumption, the machine contributes to a more environmentally friendly approach to construction.
With our extensive experience in the manufacturing industry, we provide comprehensive support and after-sales services for the Deck Floor Roll Forming Machine. Our team of skilled professionals is always on hand to offer technical assistance, training, and troubleshooting, ensuring that our customers receive uninterrupted productivity and optimum results.
In summary, the Deck Floor Roll Forming Machine represents a significant advancement in the construction machinery sector. Its precision, versatility, safety features, ease of operation, and durability make it an invaluable asset for any construction company. Our company remains committed to delivering innovative solutions that meet the evolving needs of the industry, and we are confident that this machine will revolutionize deck floor production processes.
Company News & Blog
Advanced Milling and Bending Machine for Aluminum Composite Panel Corrugated Sheets
Title: Unveiling the Power of the Corrugated Sheet Bending Machine: Revolutionizing Architectural Facades and Interior DesignIntroduction:In today's fast-paced world, innovative technologies play a crucial role in shaping our living spaces. From architectural facades to interior design, the demand for enhanced functionality and aesthetic beauty has prompted the introduction of advanced machinery. One such remarkable solution is the Aluminum Composite Panel Corrugated Sheet Bending Machine, popularly known as the Alu Bender Milling and Bending Machine. In this blog, we will dissect the revolutionary capabilities of this cutting-edge equipment, and its significance in various industries such as architectural facades, transportation, interior design, and visual communication.Understanding Corrugated Sheet Bending Machine:The Corrugated Sheet Bending Machine is an automatic milling and bending tool that specializes in processing straight edges on composite panels. Manufactured by Casadei Industria, this advanced machinery has gained immense popularity in industries where aluminum composite panels are utilized. The primary purpose of this device is to mill off the top layer of aluminum and the core of an ACM panel, thereby preparing the finished layer for bending. The automatic feeding mechanism of the machine makes the entire process seamless and efficient.Revolutionizing Architectural Facades:One of the major areas where the Corrugated Sheet Bending Machine has created a massive impact is the architectural industry, particularly in the construction of extraordinary facades. With its precise milling and bending capabilities, this machine enables architects and designers to achieve intricate and seamless designs for buildings and structures. As the top layer of aluminum is milled off, the machine ensures a flawless surface that is ready for bending. Consequently, it becomes much easier to mold the panels into desired shapes and geometries, allowing architects to unleash their creativity and give life to unique artistic visions.Transport Industry: The transport industry is another sector that significantly benefits from the Corrugated Sheet Bending Machine. With its ability to process straight edges on composite panels, this equipment proves crucial in the manufacturing of high-quality decorative exteriors for a range of vehicles, including buses, trains, and even aircraft. Additionally, the precision and speed offered by the Alu Bender Milling and Bending Machine ensure that production timelines are met consistently, thus boosting efficiency within the transport industry.Interior Design and Visual Communication:In the realm of interior design, the Corrugated Sheet Bending Machine not only enhances efficiency but also offers limitless creative possibilities. The seamless milling process performed by this machine allows for the creation of 3D elements and unique shapes that add dimension and character to interior spaces. From curved walls to intricately designed partitions, this specialized machinery empowers designers to bring their visions to life.Furthermore, the visual communication industry relies heavily on the capabilities of the Corrugated Sheet Bending Machine. By providing the means to produce visually striking signage and displays, this equipment allows businesses to attract attention and communicate their messages effectively. The precise bending process ensures that the finished layer aligns seamlessly with the core, resulting in a professional and eye-catching end product.Conclusion:The Aluminum Composite Panel Corrugated Sheet Bending Machine, or Alu Bender Milling and Bending Machine, has truly revolutionized several industries, including architectural facades, transportation, interior design, and visual communication. With its impeccable milling and bending capabilities, this advanced machinery offers unparalleled precision and efficiency, allowing for the creation of intricate designs and seamless finishes. As technology continues to shape our surroundings, the Corrugated Sheet Bending Machine stands as a testament to innovation, pushing the boundaries of creativity and functionality in the modern world.Keywords: Corrugated Sheet Bending Machine, Alu Bender Milling and Bending Machine, Aluminum Composite Panel, architectural facades, transportation, interior design, visual communication, seamless finishes, precision, efficiency, innovation.
Pros and Cons of All-In-One vs. Multiple Single Layer Roll Forming Machines: A Comprehensive Comparison
, Multiple Roll Forming Machines, All-in-one Roll Forming Machine, Double layer Roll Forming Machine, Roll Forming Machinery.When it comes to roll forming, there are a few different options to consider. One decision that needs to be made is whether to choose an all-in-one roll forming machine or multiple single layer roll forming machines. Both options have their pros and cons, so it ultimately depends on the specific needs and preferences of the user.Single layer roll forming machines are a popular choice for many manufacturers. These machines are designed to create a continuous sheet of metal by bending it into a certain shape. One of the advantages of using a single layer roll forming machine is the ability to produce a high volume of products quickly and efficiently. Since the machine only focuses on one layer at a time, it's easier to control the quality of each product and ensure that each one is consistent.Another advantage of using a single layer roll forming machine is the ability to customize the process based on the specific needs and materials being used. These machines are often designed to be highly flexible, allowing for adjustments to be made based on the thickness and type of material being used.However, one of the downsides of using a single layer roll forming machine is the need for multiple machines if a manufacturer needs to produce multiple layers. This can be a disadvantage if a manufacturer is trying to minimize the number of machines being used in their production process.On the other hand, all-in-one roll forming machines are designed to be highly versatile and efficient. These machines are capable of producing multiple layers of metal at once, which can help streamline the production process. Additionally, all-in-one roll forming machines are often designed to be highly automated, which can help reduce the need for labor and increase overall efficiency.One of the disadvantages of using an all-in-one roll forming machine is the potential for decreased quality control. Since these machines are designed to focus on multiple layers at once, it can be more difficult to ensure that each product is consistent and meets the desired quality standards.Another potential disadvantage of using an all-in-one roll forming machine is the cost. These machines are typically more expensive than single layer roll forming machines, which can be a disadvantage for smaller manufacturers or those with limited budgets.Finally, double layer roll forming machines are another option to consider. These machines are designed to produce two layers of metal at once, which can help increase production efficiency and reduce the need for multiple machines. However, like all-in-one roll forming machines, double layer roll forming machines can be more expensive and may have lower quality control.Ultimately, the decision to choose between an all-in-one roll forming machine and multiple single layer roll forming machines will depend on a variety of factors, including the specific needs and preferences of the manufacturer. Both options have their advantages and disadvantages, so manufacturers should carefully consider their options before making a final decision.
Revolutionary Fully Automatic Color Steel Roll Forming Machine Takes the Industry by Storm
Fully Automatic Roll Forming Machine Revolutionizes Color Steel ProductionIn recent years, the demand for efficient and high-quality steel construction materials has increased significantly with the accelerated pace of urbanization and industrialization. To meet this growing demand, the development of advanced machinery and manufacturing processes has become paramount. Now, a breakthrough in color steel production has been achieved with the introduction of a fully automatic roll forming machine, which promises to revolutionize the industry.Traditionally, the manufacturing of color steel products involved multiple stages, including cutting, bending, and welding. This time-consuming and labor-intensive process often resulted in inconsistent quality and high production costs. However, with the advent of the fully automatic roll forming machine, these issues are being effectively addressed.The fully automatic roll forming machine utilizes a continuous process, where a long strip of color steel is fed into the machine and then transformed into the desired shape through a series of precisely controlled rollers. This innovative technology eliminates the need for manual labor, significantly reducing production time and increasing output.One of the major advantages of this new technology is the exceptional precision it offers. With advanced computer control systems, the machine can accurately adjust the dimensions and angles of the color steel components, resulting in consistently high-quality products. This level of precision ensures that each piece can be seamlessly interconnected during construction, enhancing the durability and structural integrity of the final structures.Furthermore, the fully automatic roll forming machine can handle various types and thicknesses of color steel, allowing manufacturers to produce a wide range of products for different applications. Whether it is roofing sheets, wall panels, or steel framing elements, this machine offers the versatility required to meet diverse customer needs.In addition to its precision and versatility, the fully automatic roll forming machine also boasts impressive productivity. With its high-speed operation, it can produce several meters of color steel products per minute, greatly increasing output compared to traditional manufacturing methods. This increased efficiency translates into cost savings for manufacturers and faster delivery times for customers.The introduction of this advanced technology has not only transformed the color steel production process, but it has also revolutionized the industry as a whole. Manufacturers now have the capability to produce high-quality color steel products at a much faster pace, satisfying the growing demand for construction materials in record time.Furthermore, the fully automatic roll forming machine represents a more environmentally friendly approach to color steel production. By eliminating the need for manual labor and optimizing material usage, it minimizes waste and reduces carbon emissions. This aligns with the global trend towards sustainable manufacturing practices, making it an attractive choice for environmentally conscious companies.As a leading player in the roll forming machine industry, {} has taken the lead in developing and promoting this revolutionary fully automatic roll forming machine. With years of experience and expertise, the company has successfully engineered a state-of-the-art machine that sets new standards for efficiency, precision, and productivity in color steel production.With the adoption of this innovative technology, manufacturers can now streamline their production processes, improve product quality, and ultimately meet the growing demands of an expanding market. In conclusion, the fully automatic roll forming machine marks a significant milestone in color steel production, providing numerous benefits for manufacturers, customers, and the environment.
Leading Metal Slitting Machines for Efficient Sheet Cutting
Sheet Metal Slitting Machine Enhances Precision and Efficiency in MetalworkingIn the fast-paced world of manufacturing, precision and efficiency are paramount. It is essential for companies to have reliable and high-performing tools to meet the ever-increasing demands of the industry. Recognizing this need, an innovative solution has emerged in the form of the Sheet Metal Slitting Machine, a game-changer that enhances productivity and accuracy in metalworking.Developed by a leading technology company, this state-of-the-art machine revolutionizes the process of slitting sheet metal into narrower strips, ultimately enabling manufacturers to optimize material usage and streamline their production workflow. Gone are the days of manual labor and imprecise cutting techniques. With the Sheet Metal Slitting Machine, manufacturers can achieve remarkable results with ease.Featuring cutting-edge technology and advanced automation, this machine provides exceptional precision in slitting a wide range of materials, including stainless steel, aluminum, copper, and other alloys. The machine's computerized system ensures consistent and accurate cuts, minimizing material waste and maximizing productivity. Its high-speed operation allows for quick turnaround times, reducing production timelines and meeting tight deadlines.One of the key advantages of the Sheet Metal Slitting Machine is its versatility. It can handle various thicknesses and widths of sheet metal, catering to the specific needs of different industries. Whether it's for automotive, aerospace, construction, or any other sector, this machine can adapt to the required specifications effortlessly. With adjustable settings and customizable features, manufacturers have full control over the slitting process, resulting in superior quality output.In addition to precision and versatility, the Sheet Metal Slitting Machine ensures operator safety. Equipped with advanced safety features, such as emergency stop buttons and protective guards, it prioritizes the well-being of the people operating the machine. This commitment to safety not only instills confidence in the workforce but also helps companies comply with rigorous industry regulations and standards.Furthermore, the company behind this remarkable technology is committed to customer satisfaction and continuous improvement. With years of experience and a solid reputation in the industry, they have earned the trust of manufacturers worldwide. Their team of experts provides comprehensive support, from installation and training to maintenance and troubleshooting. Manufacturers can rely on their expertise to ensure optimal performance and longevity of the Sheet Metal Slitting Machine.As the demand for precision manufacturing continues to rise, the introduction of the Sheet Metal Slitting Machine offers a transformative solution for companies seeking enhanced efficiency and accuracy. By investing in this cutting-edge technology, manufacturers can elevate their production capabilities, reduce costs, and deliver exceptional products to the market.With its emphasis on precision, versatility, and safety, the Sheet Metal Slitting Machine represents the future of metalworking. Its advanced features empower manufacturers to stay ahead of the competition and meet the ever-evolving needs of the industry. As manufacturing processes evolve, this machine stands as a testament to innovation and progress, enabling companies to unlock their full potential and achieve new heights of success in the world of metalworking.
Discover High-Quality Roll Forming Machines from China's Top Supplier
As much as architecture has evolved over the years, the use of different materials has remained constant, one of which being steel. The durability, strength, and versatility of steel make it a go-to material for various structural applications, from high-rise buildings to residential homes. Therefore, to meet the demands of this ever-growing market, the roll forming industry has evolved and continues to extend its limits by offering innovative and modernized products. Today, we will discuss everything about the Color Steel Roll Forming Machine Factory.What is a Roll Forming Machine?A Roll Forming Machine refers to a piece of equipment that produces shapes of different sizes and profiles from metallic coils or sheets. The machine achieves this by passing these sheets through a series of rollers that gradually bend and form them into the desired shape. This process is known as roll forming, and the entire unit consists of a de-coiler, a roller system, a cutting system, and a control system. These machines offer several advantages over other manufacturing techniques, such as reduced material wastage, faster production speeds, and increased precision.What is a Color Steel Roll Forming Machine Factory?A Color Steel Roll Forming Machine Factory refers to a production facility that is specifically designed for manufacturing various types of color coated steel products. These machines provide a convenient solution for meeting the demand of the modern construction industry. The color steel material produced is attractive and durable, making it an ideal choice for the roofing, walling, and cladding systems.The Color Steel Roll Forming Machine Factory is highly flexible, which means it can produce a wide range of profiles and shapes with high precision and consistently. This flexibility, combined with the ability to customize profiles and shapes, makes it the ideal choice for architects, contractors, and manufacturers, who need to create unique products suited to their specific requirements.Features of the Color Steel Roll Forming Machine FactoryThe Color Steel Roll Forming Machine Factory is a versatile piece of equipment that can handle multiple projects. Some of the features that make it stand out include;1. High Precision and ConsistencyThe high precision and consistency of the roll forming process means that all the products produced are uniform in quality, size, and shape.2. VersatilityA color steel roll forming machine factory can create different profiles and shapes. The factory can produce panels of different profiles, including corrugated or ribbed, standing seams, box profiles, and curved products.3. Reduced Material WastageBy eliminating the need for manual cutting and forming, roll forming machines reduce the amount of wastage generated during the manufacturing process.4. High-Speed ProductionOne of the primary advantages of using a color steel roll forming machine factory is the high-speed production cycle that reduces lead times while maintaining the quality of the products.ConclusionIn conclusion, the Color Steel Roll Forming Machine Factory is an integral part of the steel industry, providing a modern and innovative alternative to traditional steel products. With a wide range of features designed to cater to the needs of the modern construction industry, the possibilities for color steel roll forming machines are endless. As a leading manufacturer of Roll Forming Machines, (brand name removed) offers high-quality machines, unmatched customer service, and competitive prices. Contact us today for further inquiries or visit our website for more information about our products and services.
Designing Auto Glazed Tile Forming Machine for Metal Roofing: Customizable Metal Roofing Roll Forming Machine
Title: Unveiling the Versatility of Color Steel Metal Glazed Tile Roll Forming MachineIntroduction:When it comes to roofing solutions, metal roof tiles have emerged as a popular choice due to their durability, versatility, and aesthetic appeal. The advent of advanced machinery, such as the Color Steel Metal Glazed Tile Roll Forming Machine, has revolutionized the production process, enabling efficient and precise manufacturing of glazed tiles for roofing sheets. In this article, we will explore the features, benefits, and applications of this innovative machine, along with its role in enhancing the overall efficiency of the metal roofing industry.1. Understanding the Color Steel Metal Glazed Tile Roll Forming Machine:The Color Steel Metal Glazed Tile Roll Forming Machine is a state-of-the-art equipment that caters to the growing demand for metal roof tiles. Designed by DAHEZB, a renowned leader in the field, this machine creates glazed tiles with exceptional precision and quality. With the ability to handle metal sheets ranging from 0.3mm to 0.6mm thickness, it offers a remarkable level of flexibility and adaptability to meet the diverse requirements of customers.2. Key Features:a) Auto Glazed Tile Forming Capability: The Color Steel Metal Glazed Tile Roll Forming Machine is equipped with an auto-glazing feature, ensuring seamless application of glazed tiles onto roofing sheets. This automated process eliminates manual intervention, maintaining consistency and saving valuable time.b) Aluminum Roofing Step Tile Machine: This advanced machine specializes in producing step-tile patterns, imparting an appealing look to the roofing surface. The unique design capabilities allow for customization, enabling customers to create roofing tiles that perfectly complement their project requirements.c) Robust Build for Enhanced Durability: Manufactured using the highest quality materials, the Color Steel Metal Glazed Tile Roll Forming Machine is built to withstand the most demanding production environments. Its robust construction ensures longevity and reliable performance, reducing downtime and maximizing productivity.3. Benefits and Advantages:a) Versatility in Material Compatibility: The Color Steel Metal Glazed Tile Roll Forming Machine is adept at working with various materials, including color steel, galvanized steel, and aluminum. This versatility allows manufacturers to cater to a wide range of customer demands, ensuring market competitiveness and expanding their product offerings.b) Speed and Efficiency: With its advanced automation features, this machine can produce high volumes of glazed tiles in a short span of time. By streamlining the production process, it significantly enhances efficiency, reducing labor costs and increasing overall output.c) Exceptional Precision and Quality: The Glazed Tile Roll Forming Machine guarantees precise dimensions, accurate designs, and consistent quality of each glazed tile produced. This level of craftsmanship enhances the final product's aesthetics and ensures customer satisfaction.4. Applications:The Color Steel Metal Glazed Tile Roll Forming Machine finds extensive application in the metal roofing industry. It is an ideal solution for commercial and residential projects that demand high-quality, long-lasting roofing systems. Its ability to produce an array of designs, patterns, and colors makes it indispensable for architects, contractors, and homeowners seeking to enrich the visual appeal of their buildings.Conclusion:The Color Steel Metal Glazed Tile Roll Forming Machine is a game-changer in the metal roofing industry, revolutionizing the production process and elevating the quality and efficiency of glazed tiles. Its unmatched versatility, durability, and precision make it the preferred choice for manufacturers and customers alike. With its ability to handle various materials and produce an array of designs, this machine signifies the future of metal roofing, where aesthetics meet functionality seamlessly.
Revolutionary Aluminum Profile Bending Machine Unveiled in Latest News
Title: Revolutionary CNC Aluminum Profile Bending Machine Transforming the Manufacturing IndustryIntroduction:In a rapidly evolving manufacturing industry, technological advancements have always played a crucial role in enhancing efficiency and precision. A groundbreaking solution has emerged in the form of a CNC Aluminum Profile Bending Machine, which is revolutionizing the way aluminum profiles are bent and shaped. By seamlessly merging technology and precision engineering, this innovative machine promises to deliver unprecedented results in terms of accuracy, speed, and versatility.Technological Features:The CNC Aluminum Profile Bending Machine is equipped with state-of-the-art computer numerical control (CNC) technology, allowing for precise control and automation of the bending process. It utilizes advanced algorithms to calculate the required bending angles, eliminating human errors and ensuring consistent quality.The machine is designed to accommodate a wide range of aluminum profiles, from simple extrusions to complex designs, catering to the diverse needs of industries such as architecture, construction, automotive, and aerospace. Its adjustable mandrel enables the bending of profiles in various sizes and shapes, offering infinite possibilities for customization.Furthermore, the CNC Aluminum Profile Bending Machine boasts a user-friendly interface, making it accessible to operators with varying levels of expertise. The intuitive controls allow for easy programming and quick set-up, reducing downtime and enhancing overall productivity.Benefits and Advantages:The introduction of this cutting-edge machine brings several benefits to the manufacturing industry, including:1. Enhanced Precision: The CNC technology ensures consistent results, minimizing deviations and errors. The machine's ability to bend aluminum profiles with exceptional accuracy and repeatability guarantees a high-quality end product.2. Improved Efficiency: By automating the bending process, the machine significantly reduces production time. Its high-speed operation enables rapid bending without compromising precision, making it ideal for large-scale manufacturing.3. Cost Savings: The CNC Aluminum Profile Bending Machine optimizes material usage, reducing waste. Its efficiency also translates into lower labor costs and increased production capacity, ultimately contributing to enhanced profitability.4. Versatility: The machine accommodates various aluminum profiles, allowing manufacturers to explore new design possibilities. It empowers engineers and designers to create complex and intricate shapes with ease, thus expanding the scope of their creative capabilities.5. Safety and Reliability: With advanced safety features and robust construction, the CNC Aluminum Profile Bending Machine prioritizes operator well-being. Its reliability ensures minimal maintenance requirements, leading to minimal downtime.Company's Commitment to Innovation:In keeping with its commitment to innovation and customer satisfaction, the company responsible for the CNC Aluminum Profile Bending Machine continually invests in research and development. It employs a team of highly skilled engineers and technicians dedicated to enhancing the machine's capabilities and exploring new possibilities for aluminum profile bending.The company possesses a solid track record, having successfully introduced several revolutionary machines to the manufacturing industry. Its relentless pursuit of excellence and customer-centric approach have earned it a reputation as a leading innovator in the field.Conclusion:The introduction of the CNC Aluminum Profile Bending Machine marks a significant technological breakthrough in the manufacturing industry. Its advanced CNC technology, precision engineering, and versatility empower manufacturers to achieve unprecedented precision, efficiency, and design possibilities. With its numerous benefits and the company's commitment to innovation, this machine is set to redefine the aluminum profile bending process and contribute to the advancement of the manufacturing sector as a whole.
Cable Tray Pultrusion Machine: Advancements in FRP Technology Shake Up the Industry
Title: Cutting-Edge FRP Cable Tray Pultrusion Machine Revolutionizes the IndustryIntroduction:Pushing the boundaries of innovation, a leading company in the manufacturing sector has recently unveiled its latest breakthrough - an advanced FRP (Fiber Reinforced Plastic) Cable Tray Pultrusion Machine. This cutting-edge technology showcases the company's commitment to providing state-of-the-art machinery solutions for the cable management industry. With a focus on enhanced productivity, efficiency, and durability, this new machine is set to revolutionize the sector in numerous ways.Paragraph 1:The FRP Cable Tray Pultrusion Machine is a result of extensive research and development, combined with the company's years of experience in the field. Pultrusion is a continuous manufacturing process that produces fiber-reinforced polymer composites with superior mechanical properties. By utilizing this innovative approach, the machine is designed to create cable trays with exceptional strength, rigidity, and resistance to environmental factors such as corrosion and fire.Paragraph 2:Implementing this advanced equipment brings forth a multitude of benefits for industries relying on cable management systems. Firstly, the FRP Cable Tray Pultrusion Machine guarantees high productivity due to its continuous and automated manufacturing process. This allows for the production of cable trays at a much faster rate compared to conventional methods, resulting in significant time and cost savings.Paragraph 3:Furthermore, the FRP Cable Tray Pultrusion Machine ensures precise and uniform product dimensions. By controlling variables such as resin content, fiber density, and temperature throughout the manufacturing process, the machine delivers cable trays with consistent quality and reliability. This feature eliminates the need for excess materials or rework, leading to further cost reduction and waste minimization.Paragraph 4:One of the most significant advantages of the FRP Cable Tray Pultrusion Machine is its durability and resistance to external influences. Traditional metal cable trays are prone to rust, corrosion, and degradation over time, affecting their performance and longevity. However, the implementation of FRP materials provides excellent resistance to corrosive substances, moisture, UV radiation, and extreme temperatures. This makes the cable trays suitable for both outdoor and indoor applications, including industrial facilities, power plants, transportation infrastructure, and more.Paragraph 5:Moreover, the FRP Cable Tray Pultrusion Machine promotes environmental sustainability by utilizing lightweight, recyclable, and non-toxic materials. The reduction in weight compared to traditional metal cable trays significantly reduces transportation costs and energy consumption during installation. Additionally, the longevity of FRP cable trays minimizes the need for replacements, preventing unnecessary waste generation.Paragraph 6:The company's commitment to customer satisfaction is reflected in the FRP Cable Tray Pultrusion Machine's user-friendly features. With its intuitive control panel and automated operation, the machine ensures ease of use and minimal training requirements for operators. This not only improves overall efficiency but also reduces human errors during the production process, leading to enhanced product quality.Conclusion:In conclusion, the introduction of the FRP Cable Tray Pultrusion Machine marks a significant milestone in the cable management industry. Through its advanced technology, this innovative machinery brings improved productivity, cost-effectiveness, and durability to cable tray manufacturing. With its ability to withstand diverse environmental conditions and promote sustainability, the FRP Cable Tray Pultrusion Machine is set to redefine the standard for cable management systems across various sectors.
Implementation of Mid-Day Meal Programme in India: A Public-Private Partnership Model
Title: Enhancing the Mid-Day Meal Programme with Akshaya Patra's Steel Patra Making MachineIntroduction:The Mid-Day Meal Programme in India has been a significant initiative implemented by the government to combat hunger and promote education. The Akshaya Patra Foundation, an NGO in India, plays a crucial role as an implementing partner of the Mid-Day Meal Scheme. With steadfast support from various stakeholders, including corporate donors, Akshaya Patra is revolutionizing the meal preparation process through the introduction of cutting-edge technology such as the Steel Patra Making Machine. In this blog post, we will delve into the Akshaya Patra Foundation's journey in implementing the Mid-Day Meal Programme and explore the remarkable impact of the Steel Patra Making Machine.Akshaya Patra's Role in the Mid-Day Meal Programme:The Akshaya Patra Foundation, founded in 2000, operates with a robust public-private partnership (PPP) model. It endeavors to provide wholesome meals to millions of underprivileged children across India, thereby encouraging regular school attendance and enhancing their overall well-being. As an implementing partner of the Mid-Day Meal Scheme, Akshaya Patra plays a critical role in ensuring the successful execution of this ambitious program.Steel Patra Making Machine: Revolutionizing Meal PreparationOne of the key challenges faced by Akshaya Patra during the early stages of the programme was the need for efficient, time-saving, and hygienic meal preparation methods. Traditional cooking methods, involving large vessels and wood-fired stoves, were not conducive to serving nutritious meals to millions of children every day. Recognizing this obstacle, the foundation collaborated with corporate donors to develop the Steel Patra Making Machine.This innovative piece of equipment has significantly transformed the meal preparation process, making it more streamlined and efficient. The machine applies advanced technology to automate the production of stainless steel cooking pots (or Patras) used for cooking the Mid-Day Meals. These standardized Patras ensure consistency in cooking, diminish the risk of contamination, and enhance the overall hygiene quotient of the meals provided.Impressive Features and Benefits of the Steel Patra Making Machine:1. Time-Saving: The automated process of the Steel Patra Making Machine expedites the production of cooking pots. This saves valuable time for the Akshaya Patra team, enabling them to serve meals to more children within the stipulated time.2. Standardization: The machine ensures uniformity in the size and quality of the Patras, eliminating variations in the cooking process. This not only enhances the taste of the meals but also optimizes the resource utilization, resulting in cost efficiency.3. Hygiene and Safety Measures: Stainless steel Patras are not only durable but also offer superior hygiene due to their non-reactive nature. The Steel Patra Making Machine produces stainless steel Patras that are easy to clean and maintain, thereby minimizing the risk of cross-contamination and ensuring safe meals for children.4. Scalability: The machine's capability to produce a large number of standardized Patras enables the Akshaya Patra Foundation to seamlessly expand its operations and reach out to more schools and children. This scalability is crucial for effectively tackling malnutrition and maximizing the impact of the Mid-Day Meal Programme.Conclusion:The Akshaya Patra Foundation's implementation of the Mid-Day Meal Programme has been significantly reinforced by the introduction of the Steel Patra Making Machine. Through this innovative technology, the foundation has overcome numerous logistical challenges and enhanced the overall efficiency, hygiene, and safety of the meal preparation process. As a result, Akshaya Patra continues to make an invaluable contribution to the lives of millions of children in need across India.When organizations and individuals collaborate to develop sustainable solutions, like the Steel Patra Making Machine, we can create a positive ripple effect that benefits society as a whole. Akshaya Patra's journey stands as a testament to the immense potential of public-private partnerships in transforming lives and fostering a better future for generations to come.Keywords: Akshaya Patra Foundation, Mid-Day Meal Programme, public-private partnership, Steel Patra Making Machine, meal preparation, hygiene, automation, efficiency, scalability, nutrition.