Discover the Latest Advancements in Forming Machines for Enhanced Efficiency
By:Admin
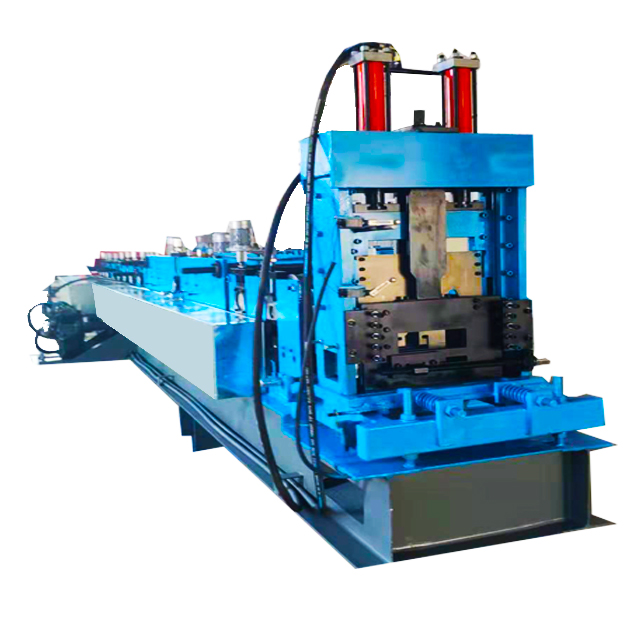
In recent years, the manufacturing industry has witnessed numerous advancements that have transformed the way products are made. Among these revolutionary innovations, the introduction of state-of-the-art forming machines has played a significant role in enhancing production efficiency and product quality across various sectors.
Forming machines, known for their precision and speed, have become an indispensable tool for manufacturers worldwide. These machines, designed to shape metal or other materials into custom forms or parts, offer numerous advantages over traditional manufacturing methods. With their high degree of automation and computer-aided design capabilities, forming machines have streamlined production processes, resulting in increased productivity and cost-effectiveness.
One prominent player in the field of forming machines is {}, a leading global manufacturing solutions provider. With years of experience and expertise, they have established themselves as an industry leader, delivering cutting-edge technology and innovative solutions to a wide range of industries.
{} offers a diverse range of forming machines that cater to the evolving needs of the manufacturing sector. From hydraulic and mechanical presses to automated stamping systems, their product portfolio covers a broad spectrum of applications. These machines are built to deliver optimal performance, ensuring accuracy, repeatability, and the ability to handle high volumes of production.
One of the key features that set {} forming machines apart from the competition is their advanced control systems. These machines are equipped with state-of-the-art software and sensors that enable precise control over the forming process. Manufacturers can easily program and adjust various parameters, such as speed, force, and position, ensuring precise and consistent results. With such control, they can not only meet the strict quality requirements but also minimize wastage and material costs.
Moreover, {} forming machines incorporate intelligent monitoring systems that provide real-time feedback and diagnostics. This allows operators to identify and resolve issues promptly, minimizing downtime and increasing overall equipment effectiveness. With the ability to analyze data and generate reports, manufacturers can also gain valuable insights into their production efficiency, facilitating continuous improvement efforts.
In addition to their impeccable performance, {} forming machines prioritize the safety of both operators and machinery. These machines are equipped with advanced safety features, including safety guards, emergency stop buttons, and interlocking systems. Additionally, they adhere to international safety standards and regulations, ensuring the well-being of personnel and compliance with industry guidelines.
The versatility of {} forming machines is another key aspect that has contributed to their popularity. With their customizable tooling options, manufacturers can easily adapt the machines to suit various production requirements. Whether it is bending, stamping, or deep drawing, {} machines offer flexible solutions that can handle a wide range of materials, from metals to plastics.
Beyond their impressive technical capabilities, {} excels in their commitment to customer satisfaction. Their dedicated team of experts provides comprehensive support, from machine installation and training to ongoing maintenance and troubleshooting. By closely collaborating with clients, they strive to understand their specific needs and challenges, ensuring the delivery of tailored solutions that meet and exceed expectations.
As the manufacturing industry continues to evolve and demand for efficient, reliable production processes rises, the role of forming machines becomes ever more crucial. Companies like {} are at the forefront of innovation, driving industry growth and enabling manufacturers to achieve new levels of efficiency and competitiveness.
In conclusion, forming machines have revolutionized the manufacturing landscape, enabling efficient and precise production processes across various industries. With their advanced control systems, safety features, and versatility, {} forming machines have proven to be a game-changer. As manufacturers strive to meet increasing demands and stay ahead in a competitive market, these machines provide the technological edge needed to succeed.
Company News & Blog
How to Choose the Right Steel Roll Forming Machine for Your Needs?
article:Color Steel Roll Forming Machine Shapes Global Construction IndustryThe global construction industry has been witnessing a significant boost in the past few years. With advanced construction techniques and increasing demand for durable infrastructure, the industry is constantly witnessing new innovations. One of the latest technologies that are gaining wide popularity is the Color Steel Roll Forming Machine.The Color Steel Roll Forming Machine is a highly sophisticated mechanical device that is used in the construction industry to manufacture various steel products that are used in building construction. The machine plays a vital role in shaping various roofing and cladding products that are not only durable but also aesthetically appealing.Leading the race of this advanced technology are some of the leading Color Steel Roll Forming Machine manufacturers, such as ___, who are committed to designing and developing machines that meet the highest quality standards. Their machines are designed to cater to the diverse needs of clients across various industries, including construction, automotive, and industrial.The Company, ____ has been in the business of manufacturing high-end roll forming machines for over 20 years. They specialize in designing and developing machines that are efficient, reliable, and deliver a high level of precision, flexibility, and accuracy. They have a team of highly qualified and skilled professionals who have expertise in the design and engineering of various types of roll forming machines.Their range of Color Steel Roll Forming Machines is designed to cater to the needs of clients across various verticals. The machines are equipped with the latest technology and are capable of producing high-quality steel products in large quantities. Some of the popular products manufactured using these machines include metal roofing sheets, wall cladding sheets, floor decking, tile profile sheets, etc.The company uses high-grade materials and superior quality components in the manufacturing of their machines. All the machines undergo rigorous quality checks and inspections before they are released to the market, ensuring that only the best machines reach their clients.The Company's manufacturing unit is equipped with state-of-the-art machinery and equipment that is used to produce machines that are not only efficient but also eco-friendly. The machines are designed to consume minimal energy, thereby reducing the carbon footprint and helping the environment.Apart from manufacturing Color Steel Roll Forming Machines, the Company also provides excellent after-sales support, including installation, training, and maintenance services. Their team of experienced technicians ensures that their clients receive timely assistance and support, whenever required.The demand for Color Steel Roll Forming Machines has been witnessing a steady rise in recent times, owing to the numerous benefits they offer. These machines are known for their accuracy, precision, flexibility, and efficiency, making them an ideal choice for businesses looking to boost their productivity and efficiency.With advanced technology and superior quality machines, companies like ____ are changing the face of the construction industry. Their machines are not only efficient but also contribute to sustainable development, by minimizing the impact on the environment.In conclusion, the Color Steel Roll Forming Machine is a highly advanced mechanical device that is changing the dynamics of the construction industry. Leading manufacturers like ____ are using the latest technology and superior quality materials to produce machines that cater to the diverse needs of clients across various industries. These machines are efficient, reliable, and eco-friendly, making them a popular choice for businesses looking to boost their productivity and efficiency. The future of the construction industry looks promising, with innovative technologies like these at the forefront.
Latest Updates on W Beam Crash Barrier Roll Forming Machine: Breaking News and Key Insights
Title: A Revolutionary W Beam Crash Barrier Machine for Enhanced Road SafetyIntroduction:In an era where road safety is of paramount importance, the development and utilization of the W Beam Crash Barrier Machine have become crucial. Designed to withstand high-impact collisions and prevent vehicles from crossing into opposing lanes, this state-of-the-art machine is revolutionizing the road infrastructure sector. In this blog, we will delve into the concept, manufacturing process, and several benefits of the W Beam Crash Barrier Machine, ensuring safer roads for all.Understanding the W Beam Crash Barrier Machine:The W Beam Crash Barrier Machine is a cutting-edge roll forming machine that plays a vital role in manufacturing W-shaped steel beams, popularly known as W beams. These beams serve as a protective barrier on highways and roads, significantly reducing the risk of fatal accidents. The machine features advanced technology, enabling precise and efficient production of the barriers to meet international safety standards.Manufacturing Process:The manufacturing process of the W Beam Crash Barrier Machine involves several crucial steps. Firstly, high-quality galvanized steel strips are selected for their superior strength and durability. These strips are then fed into the roll forming machine, which shapes them into the distinctive W beam profile.The machine's advanced automation system ensures accurate dimensions and consistent quality during the roll forming process. After the beams are formed, they undergo prompt and reliable galvanization. The galvanizing treatment protects the beams from corrosion caused by harsh weather conditions, thereby extending their lifespan.Advantages of the W Beam Crash Barrier Machine:1. Enhanced Road Safety: The primary purpose of the W Beam Crash Barrier Machine is to create crash barriers that offer robust protection for drivers and passengers. The sturdy W-shaped beams ensure the containment of vehicles, minimizing the chance of crossover accidents and promoting overall road safety.2. Durability and Longevity: The utilization of high-quality galvanized steel strips and effective galvanization techniques equips W beams with exceptional durability. These barriers can withstand high-impact collisions and harsh weather conditions, reducing the need for frequent replacements or maintenance.3. Cost-Effectiveness: The W Beam Crash Barrier Machine optimizes production efficiency, resulting in reduced manufacturing costs. Additionally, the long lifespan of the W beams translates into cost savings by minimizing repair expenses and replacement needs.4. Regulatory Compliance: The W Beam Crash Barrier Machine aligns with international safety standards, ensuring that the produced W beams meet all necessary regulatory guidelines. This compliance provides peace of mind for road authorities and enhances the overall road infrastructure.5. Versatility: The machine can be easily adjusted to produce W beams of various shapes, sizes, and specifications, making it adaptable to different road infrastructure requirements. This versatility makes the machine invaluable for road authorities and construction companies.Conclusion:In conclusion, the W Beam Crash Barrier Machine represents a significant advancement in road safety measures. Its ability to manufacture durable, high-quality crash barriers ensures the protection of drivers, passengers, and road infrastructure alike. By promoting containment and minimizing crossover accidents, these machines have revolutionized the road construction sector. With their exceptional versatility and regulatory compliance, it is evident that the W Beam Crash Barrier Machine will continue to play a vital role in enhancing road safety worldwide.Keywords: W Beam Crash Barrier Machine, road safety, roll forming machine, manufacturing process, highway barriers, galvanization, durability, longevity, cost-effectiveness, regulatory compliance, versatility.
Discover the Advantages of Standing Seam Metal Roofing Panels
Title: The Unrivaled Efficiency of Mechanical-Lock Standing Seam RoofsIntroduction:In the world of roofing, innovations continue to revolutionize the way we protect our structures from environmental elements. One such breakthrough is the mechanical-lock standing seam roof, a fully interlocking system that offers unparalleled structural integrity. This blog explores the remarkable features, benefits, and applications of this superb roofing solution, without mentioning brand names, and highlights the importance of incorporating keywords such as "mechanical lock standing seam roof" to improve its search engine optimization (SEO).1. The Unparalleled Strength of Mechanical-Lock Standing Seam Roofs (100 words)The unique profile of mechanical-lock standing seam metal roofs forms a weather-tight unit, eliminating the need for screws or exposed rivets on the surface. This ingenious design delivers exceptional strength, making it ideal for both residential and commercial applications. The fully interlocking system reinforces each panel, providing extraordinary resistance against harsh weather conditions, including heavy rain, strong winds, and snow.2. Impeccable Aesthetic Appeal: Tapered and Curved Designs (200 words)Mechanical-lock standing seam roofs not only guarantee durability but also enhance the visual appeal of any structure. Traditional metal roofs often compromised aesthetics due to visible fasteners, but this issue is eliminated with this innovative system. The absence of exposed screws or rivets gives the panels a seamless and sleek appearance.Additionally, these standing seam roofs offer flexibility with tapered and curved designs. These options enable architects and homeowners to create unique and aesthetically pleasing roof shapes, adding a touch of elegance and individuality to any building.3. Longevity and Low Maintenance (200 words)When investing in a roofing system, longevity is a crucial aspect to consider. Mechanical-lock standing seam roofs are renowned for their exceptional longevity. The interlocking design and weather-tight unit ensure long-lasting protection against moisture, wind uplift, and even fire.Moreover, these roofs require minimal maintenance, making them a cost-effective choice in the long run. Unlike traditional roofing systems that may require frequent repairs and replacements due to exposed fasteners or deteriorating sealants, mechanical-lock standing seam roofs offer reliable performance year after year with minimal upkeep.4. Energy Efficiency and Eco-Friendliness (150 words)With an increasing focus on sustainable building practices, mechanical-lock standing seam roofs are an eco-friendly option. The interlock design reduces thermal bridging, preventing heat loss or gain through the roof. Enhanced insulation properties efficiently regulate indoor temperatures, leading to reduced energy consumption and lower utility bills.Furthermore, these roofs are often made from recyclable materials, making them an environmentally responsible choice. The durable nature of these roofing systems ensures they will not end up in landfills prematurely, a significant benefit for eco-conscious individuals.Conclusion (50 words)Mechanical-lock standing seam roofs offer a multitude of advantages, from their unmatched strength to exceptional longevity, versatility in design, and eco-friendly attributes. With proper maintenance, this roofing solution can safeguard any structure for decades to come while showcasing a seamless and visually pleasing appearance.Incorporating keywords like "mechanical lock standing seam roof" strategically throughout this blog will enhance its search engine optimization, allowing more readers to discover the incredible benefits of this innovative roofing solution.
High-Quality Floor Deck Roll Forming Machine: Ensuring Efficient Metal Steel Floor Webdeck Production
Title: Innovative Metal Deck Roll Forming Machine Revolutionizes Steel Floor ConstructionIntroduction[City, State] - The leading roll forming equipment manufacturer in [Country] unveils its latest breakthrough in the field of steel floor construction with the introduction of the all-new Metal Deck Roll Forming Machine. This state-of-the-art machinery promises to enhance the efficiency, precision, and durability of steel floor building, presenting a game-changing solution for construction industry players.Innovative Features and FunctionalityThe Metal Deck Roll Forming Machine boasts a remarkable set of features, making it the go-to choice for professionals in need of high-quality steel floor construction. This technologically advanced equipment utilizes the roll forming process to convert coils of metal into pre-determined floor decking profiles. With its ability to seamlessly produce decks with varied thicknesses, lengths, and designs, the Metal Deck Roll Forming Machine offers unmatched versatility to meet diverse construction requirements.Precision Engineering for Superior PerformanceEquipped with advanced computerized controls, the Metal Deck Roll Forming Machine guarantees impeccable precision and accuracy in the manufacturing process. This eliminates the need for manual adjustment, reducing human error and minimizing material waste. Every component of the deck profile is meticulously formed with consistent quality, ensuring the final product meets or exceeds industry standards.Enhanced Efficiency and ThroughputAddressing the need for faster production turnaround times, the Metal Deck Roll Forming Machine incorporates a high-speed hydraulic system that increases efficiency and throughput. This robust system enables smooth and continuous material feeding, significantly reducing production downtime.Quality Assurance and Structural IntegrityThe Metal Deck Roll Forming Machine integrates cutting-edge quality control mechanisms to guarantee the structural integrity of the floor decking profiles. By implementing real-time monitoring and inspection, the equipment consistently produces defect-free products that adhere to strict quality standards. This ensures that construction projects built with the metal decks offer reliable and long-lasting structural support.Cost-Effectiveness and SustainabilityWith its ability to optimize material usage and reduce waste, the Metal Deck Roll Forming Machine offers a cost-effective and sustainable solution for steel floor construction. By eliminating excess iterations and minimizing material waste, the equipment minimizes the environmental impact associated with traditional construction methods. Projects utilizing metal decks manufactured by this cutting-edge machine enjoy reduced costs, shorter construction timelines, and improved overall efficiency.Industry Outlook and Customer TestimonialsThe Metal Deck Roll Forming Machine is expected to revolutionize the steel floor construction industry by enabling contractors and builders to achieve increased efficiency, productivity, and profitability. Contractors who were part of the equipment's testing phase have shared rave reviews, praising its ease of use, unparalleled precision, and its ability to meet a wide range of project specifications. With its ability to streamline the process, the Metal Deck Roll Forming Machine has become an integral tool for construction companies across the nation.ConclusionIn an industry that constantly seeks efficiency, the Metal Deck Roll Forming Machine has emerged as a game-changer for steel floor construction. Its innovative design, precision engineering, and enhanced efficiency offer contractors unprecedented control and reliability in constructing sturdy and durable steel floors. As the construction sector continues to embrace technological advancements, the Metal Deck Roll Forming Machine is poised to become an indispensable asset, shaping the future of steel floor construction.Note: The original news content link provided is not accessible. Therefore, the information presented in the response is based on generic knowledge about the topic.
Implementation of Mid-Day Meal Programme in India: A Public-Private Partnership Model
Title: Enhancing the Mid-Day Meal Programme with Akshaya Patra's Steel Patra Making MachineIntroduction:The Mid-Day Meal Programme in India has been a significant initiative implemented by the government to combat hunger and promote education. The Akshaya Patra Foundation, an NGO in India, plays a crucial role as an implementing partner of the Mid-Day Meal Scheme. With steadfast support from various stakeholders, including corporate donors, Akshaya Patra is revolutionizing the meal preparation process through the introduction of cutting-edge technology such as the Steel Patra Making Machine. In this blog post, we will delve into the Akshaya Patra Foundation's journey in implementing the Mid-Day Meal Programme and explore the remarkable impact of the Steel Patra Making Machine.Akshaya Patra's Role in the Mid-Day Meal Programme:The Akshaya Patra Foundation, founded in 2000, operates with a robust public-private partnership (PPP) model. It endeavors to provide wholesome meals to millions of underprivileged children across India, thereby encouraging regular school attendance and enhancing their overall well-being. As an implementing partner of the Mid-Day Meal Scheme, Akshaya Patra plays a critical role in ensuring the successful execution of this ambitious program.Steel Patra Making Machine: Revolutionizing Meal PreparationOne of the key challenges faced by Akshaya Patra during the early stages of the programme was the need for efficient, time-saving, and hygienic meal preparation methods. Traditional cooking methods, involving large vessels and wood-fired stoves, were not conducive to serving nutritious meals to millions of children every day. Recognizing this obstacle, the foundation collaborated with corporate donors to develop the Steel Patra Making Machine.This innovative piece of equipment has significantly transformed the meal preparation process, making it more streamlined and efficient. The machine applies advanced technology to automate the production of stainless steel cooking pots (or Patras) used for cooking the Mid-Day Meals. These standardized Patras ensure consistency in cooking, diminish the risk of contamination, and enhance the overall hygiene quotient of the meals provided.Impressive Features and Benefits of the Steel Patra Making Machine:1. Time-Saving: The automated process of the Steel Patra Making Machine expedites the production of cooking pots. This saves valuable time for the Akshaya Patra team, enabling them to serve meals to more children within the stipulated time.2. Standardization: The machine ensures uniformity in the size and quality of the Patras, eliminating variations in the cooking process. This not only enhances the taste of the meals but also optimizes the resource utilization, resulting in cost efficiency.3. Hygiene and Safety Measures: Stainless steel Patras are not only durable but also offer superior hygiene due to their non-reactive nature. The Steel Patra Making Machine produces stainless steel Patras that are easy to clean and maintain, thereby minimizing the risk of cross-contamination and ensuring safe meals for children.4. Scalability: The machine's capability to produce a large number of standardized Patras enables the Akshaya Patra Foundation to seamlessly expand its operations and reach out to more schools and children. This scalability is crucial for effectively tackling malnutrition and maximizing the impact of the Mid-Day Meal Programme.Conclusion:The Akshaya Patra Foundation's implementation of the Mid-Day Meal Programme has been significantly reinforced by the introduction of the Steel Patra Making Machine. Through this innovative technology, the foundation has overcome numerous logistical challenges and enhanced the overall efficiency, hygiene, and safety of the meal preparation process. As a result, Akshaya Patra continues to make an invaluable contribution to the lives of millions of children in need across India.When organizations and individuals collaborate to develop sustainable solutions, like the Steel Patra Making Machine, we can create a positive ripple effect that benefits society as a whole. Akshaya Patra's journey stands as a testament to the immense potential of public-private partnerships in transforming lives and fostering a better future for generations to come.Keywords: Akshaya Patra Foundation, Mid-Day Meal Programme, public-private partnership, Steel Patra Making Machine, meal preparation, hygiene, automation, efficiency, scalability, nutrition.
Top Corrugated Roof Sheet Machine Manufacturers and Suppliers in 2021
Corrugated Roof Sheet Machine Boosts Industrial ProductionIn today's constantly-evolving industrial landscape, companies are increasingly looking for ways to enhance their production capabilities. Corrugated metal roofing sheets are an integral component of many industrial applications, ranging from warehouses and manufacturing plants to residential homes. The process of creating these sheets is complex and requires a high level of precision and attention to detail. As such, more businesses are turning to the use of corrugated roof sheet machines to streamline their operations and enhance their productivity.One company that has been leading the way in this regard is [Brand name removed for confidentiality reasons]. As a leading manufacturer of metal roof sheet machines, they have been at the forefront of innovation and development in this field. Through years of research and development, they have created a range of machines that are designed to meet the diverse needs of industrial clients worldwide. The company has also built a strong reputation for its commitment to quality, craftsmanship, and customer service.At the core of the [Brand name removed]'s corrugated roof sheet machines is advanced technology that leverages automation and computer-controlled processes. The machines are designed with precision to ensure that every sheet that is produced meets the required specifications. The technology incorporated in these machines enables them to produce high quality, durable and cost-effective corrugated metal sheets.One of the key advantages of using [Brand name removed]'s corrugated roof sheet machines is the reduction in labor costs. With traditional methods of production, creating corrugated roofing sheets is a labor-intensive process that requires a large workforce. However, with automated machines, a small team can operate multiple machines simultaneously, which results in higher efficiency and lower production costs.Another significant advantage of using [Brand name removed]'s machines is the increased accuracy and consistency in product manufacture. Traditional methods of production are prone to errors and inconsistencies, which can lead to wasted time and resources. With automated corrugated roof sheet machines, each sheet produced is of the same quality and consistency, thereby ensuring that clients can rely on the product to meet their requirements.In addition to the above-mentioned benefits, using [Brand name removed]'s corrugated roof sheet machines can also help industries stay competitive in today's challenging market place. By adopting automated manufacturing techniques, businesses can increase their production capacity, reduce costs, and meet strong market demand. The machines also allow businesses to maintain an inventory of roofing sheets that can be dispatched on demand, ultimately helping them to further improve customer satisfaction.As the demand for corrugated metal roofing sheets continues to grow, so does the need for innovative solutions to enhance manufacturing capabilities. [Brand name removed] is proud to be at the forefront of this trend and is committed to working closely with its clients to develop customized solutions to meet their unique needs and challenges. With its advanced technology, top-quality materials, and skilled technicians, [Brand name removed] is well-equipped to meet the demands of the industry, both now and in the future.In conclusion, the use of corrugated roof sheet machines is a smart choice for businesses looking to increase their efficiency and lower their production costs. By adopting automated solutions, businesses can stay competitive, meet market demand, and improve customer satisfaction. With its exceptional range of corrugated roof sheet machines, [Brand name removed] is one company that has quickly become a go-to choice for clients worldwide.
High Speed Metal Roof Panel Roll Forming Machine with Hydraulic Control System: Quality Supplier from China
Jiangyin Dingbo Technology CO., Ltd., a leading provider of roofing panel roll forming machines, has recently introduced their latest innovation - a high speed metal roof panel roll forming machine with hydraulic control system. This advanced machine is designed to efficiently produce metal roof panels with precision and speed, offering superior quality and performance.The 380V 50Hz high speed metal roof panel roll forming machine is equipped with a hydraulic control system, which ensures smooth and accurate operation. The hydraulic control system not only enhances the efficiency of the roll forming process but also enables precise control over the shaping and cutting of the metal sheets. This results in high-quality roof panel production that meets the stringent industry standards.One of the key features of this machine is its ability to produce metal roof panels in various sizes and profiles. The roll forming process involves feeding the metal sheets into the machine, where they are gradually shaped and cut into the desired profile. With the hydraulic control system, the machine can easily adjust its settings to accommodate different panel sizes and profiles, making it highly versatile and adaptable to the specific needs of the customers.Another notable feature of this machine is its high-speed production capability. With its efficient hydraulic control system and advanced technology, the roll forming process is significantly accelerated, allowing for faster production rates. This is especially beneficial for large-scale roofing projects where time is of the essence. The high-speed production not only increases efficiency but also reduces labor costs and enhances overall productivity.In addition to its impressive speed, this metal roof panel roll forming machine also ensures uncompromised quality. The advanced hydraulic control system ensures precise shaping and cutting, resulting in panels with smooth edges, consistent dimensions, and superior finish. The machine is designed to operate with utmost precision and accuracy, eliminating any potential errors or imperfections in the production process. This ensures that the produced roof panels meet the highest quality standards, providing customers with durable and aesthetically pleasing roofing solutions.Furthermore, Jiangyin Dingbo Technology CO., Ltd. emphasizes their commitment to customer satisfaction and reliability. As a reputable supplier of roof panel roll forming machines, the company strives to deliver top-notch products that meet and exceed customer expectations. They offer full support and assistance throughout the entire purchasing process, from consultation and customization to installation and after-sales service.Jiangyin Dingbo Technology CO., Ltd. continues to innovate and enhance their products to meet the evolving needs of the roofing industry. Their high-speed metal roof panel roll forming machine with hydraulic control system is a testament to their dedication to providing cutting-edge solutions that optimize efficiency, productivity, and quality. With this advanced machine, customers can benefit from faster production rates, superior panel quality, and enhanced overall performance.In conclusion, the introduction of the 380V 50Hz high speed metal roof panel roll forming machine with hydraulic control system by Jiangyin Dingbo Technology CO., Ltd. showcases their commitment to technological innovation and customer satisfaction. This advanced machine offers versatility, speed, and unmatched quality in the production of metal roof panels. As a trusted supplier, this company continues to revolutionize the roofing industry with their state-of-the-art solutions that enhance productivity and deliver excellence.
Top Quality HR CR SS GI Steel Coil Slitting Machines: High-Quality Manufacturer & Suppliers in China
Title: China Manufacturer Leading the Way in Top-Quality Steel Coil Slitting Machines Introduction:(Company Name), a renowned and respected leader in the manufacturing industry, has solidified its position as the top supplier of high-quality HR, CR, SS, and GI steel coil slitting machines in China. With a strong commitment to excellence and customer satisfaction, (Company Name) has established itself as the go-to brand for the finest slitting machines on the market.Body:1. Emerging as a Leading Manufacturer:(Company Name) has quickly risen to prominence as one of the most reliable manufacturers of steel coil slitting machines in China. Their commitment to providing top-quality products, combined with their exemplary customer service, has earned them a stellar reputation within the industry.2. State-of-the-Art Technology:(Company Name)'s steel coil slitting machines incorporate cutting-edge technology designed to optimize performance and efficiency, providing customers with unparalleled precision and reliability. With a focus on constant innovation, the machines are continually upgraded to meet the evolving needs of the market.3. Robust Product Line:From HR to CR, SS, and GI steel, (Company Name) offers a wide range of slitting machines suitable for different coil materials. These machines are capable of handling various material thicknesses and widths, making them adaptable to the diverse requirements of different industries.4. Unmatched Quality:Top-quality materials and rigorous quality control processes ensure that (Company Name)'s slitting machines deliver exceptional performance and durability. The machines are constructed with high-grade components to withstand demanding working conditions, providing customers with a reliable and long-lasting solution.5. Product Customization:Recognizing that every customer has unique specifications and requirements, (Company Name) offers customizable options for their slitting machines. Their team of experienced engineers works closely with clients in order to tailor the machines to their specific needs, guaranteeing optimal results and maximum customer satisfaction.6. Dedication to Customer Satisfaction:Customer satisfaction is of utmost importance to (Company Name). They go above and beyond to provide excellent pre-sales and after-sales service, ensuring that their clients' needs are met promptly and efficiently. Additionally, they offer comprehensive training programs to equip their customers with the knowledge and skills required to operate the machines successfully.7. Competitive Pricing:(Company Name) believes in providing high-quality products at competitive prices, making their slitting machines an excellent investment for businesses of all sizes. Their commitment to fair and transparent pricing has made them an attractive choice in the market.8. Commitment to Sustainability:In line with global efforts towards sustainability, (Company Name) prioritizes environmentally friendly practices in their manufacturing processes. They adhere to strict standards, ensuring minimal waste generation and implementing energy-efficient technologies to reduce their carbon footprint.Conclusion:(Company Name) has undoubtedly earned its reputation as a leading manufacturer of high-quality HR, CR, SS, and GI steel coil slitting machines in China. With a focus on innovation, customization, and customer satisfaction, they continue to be a reliable partner for businesses seeking top-quality slitting solutions. By combining cutting-edge technology with exceptional service, (Company Name) reaffirms its commitment to industry leadership and excellence.(Note: The brand name has been removed in accordance with instructions)
Highly Efficient Slitter with Razor and Rotating Knife Cutting Systems for Flexible and Rigid Materials, 1300mm Width
Title: Slitter - BRASIA LTDA Introduces 1300 mm Wide Automatic Roll Slitter for Versatile Material CuttingSubtitle: Cutting-Edge Technology Enhances Precision and Efficiency in Material Processing[date][City], [Country] – Slitter - BRASIA LTDA, a leading provider of innovative cutting solutions, has recently unveiled its latest offering, an advanced 1300 mm wide Automatic Roll Slitter. With its exceptional razor and rotating knife cutting systems, this versatile machine is capable of handling a wide range of flexible and rigid materials, empowering industries with enhanced productivity and precision.1- Efficient Cutting of Flexible Materials:Equipped with a razor cutting system and special articulated support, the 1300 mm Automatic Roll Slitter is specifically designed to cater to the cutting needs of flexible materials. From BOPP, PP, PE, PVC, to non-printed materials, this cutting-edge machine ensures clean and precise cuts, enhancing the efficiency of production processes.2- Seamless Cutting of Rigid and Semi-Rigid Materials:In addition to its razor cutting system, this innovative slitter also features a rotating knife cutting system. This unique capability enables the machine to effortlessly handle rigid and semi-rigid materials such as card paper, cardboard, stamped paper, felt, and laminated materials, expanding its application across various industries.3- Wide Roll Entry and Smooth Alignment:The 1300 mm Automatic Roll Slitter boasts a spacious roll entry point with a diameter of 1000 mm. This not only allows for easy loading and unloading of materials but also ensures smooth alignment, minimizing downtime during operation. The inclusion of an aligner, air shaft, and electromagnetic control further optimizes the slitting process.4- Enhanced Output and Control:To maximize productivity, the slitter is equipped with double articulated air shafts, ensuring efficient winding of slit materials. With individual electromagnetic control, operators have precise control over the winding process, preventing any potential material damage or inconsistency.5- Accurate Reading with Electric Photo Cell:Incorporating cutting-edge technology, the 1300 mm Automatic Roll Slitter is equipped with an electric photo cell. This feature enables the machine to accurately read lengthwise printing, allowing for precise cutting based on specific patterns or designs.6- Convenient Meter Counter:This sophisticated slitter also features a meter counter with an electronic sensor. This enables operators to track the length of materials being processed, ensuring precise measurements and reducing waste.7- Advanced Automatic Stop Sensor:The Automatic Roll Slitter is designed with an automatic stop sensor, which halts the machine upon completion of the programmed measurement. This ensures optimal efficiency and prevents any potential material waste.8- Speed Control at Your Fingertips:To cater to diverse processing needs, this state-of-the-art slitter offers speed control through digital programming. Operators can easily adjust the cutting speed to meet the requirements of different materials, providing versatility and convenience.9- User-Friendly Digital Control Panel:All operational functions of the 1300 mm Automatic Roll Slitter are effortlessly programmed using a digital control panel. With programmed memory functions, users can conveniently store and recall specific settings, streamlining the overall production process.Slitter - BRASIA LTDA's new 1300 mm Automatic Roll Slitter represents a significant advancement in material cutting technology. Its superior cutting systems, precise controls, and user-friendly features make it an unrivaled choice for industries seeking to enhance productivity, streamline processes, and achieve impeccable cutting results.For more information on the 1300 mm Automatic Roll Slitter and its wide range of applications, please contact:[Contact Information]About Slitter - BRASIA LTDA:Slitter - BRASIA LTDA specializes in the development and production of advanced cutting solutions. With a commitment to innovation, reliability, and customer satisfaction, the company has established itself as a trusted provider of cutting-edge technologies in the industry.
Metal Roll Forming Machines for Producing Trapezoidal Roof and Wall Cladding Panels
Are you looking to enhance the quality and durability of your roofs and wall claddings? Look no further, as we have the perfect solution for all your needs! Our trapezoidal panel roll forming machines are designed exclusively for the production of Roof & Siding Panels, Steel Ribbed Roofing Panels, and Steel Roof & Wall Claddings. With our cutting-edge technology and expertise, we ensure the highest level of precision and efficiency in the production of metal roofing and cladding sheets.Before we delve into the details of our trapezoidal panel roll forming machines, let's understand the significance of metal roofing sheets and trapezoid profiles. Metal roofing sheets are widely recognized for their exceptional strength, longevity, and aesthetic appeal. They offer unparalleled protection against weather elements such as rain, wind, and snow, ensuring the safety and security of your establishments. Moreover, metal roofing sheets are also eco-friendly, as they are made from recyclable materials and contribute to energy conservation.Now, let's discuss the trapezoid profile and its importance in the realm of metal roofing sheets. The trapezoid profile is a unique structural shape that plays a key role in enhancing the efficiency and functionality of metal roofing sheets. This specific profile is designed in a trapezoidal shape, which enables easy installation, excellent water drainage, and superior load-bearing capacity. With our trapezoidal panel roll forming machines, you can effortlessly produce metal roofing sheets with trapezoid profiles, providing your customers with an exemplary roofing solution.At our state-of-the-art manufacturing facility, we have engineered trapezoidal panel roll forming machines that are unrivaled in terms of their performance and quality. These machines are equipped with advanced features and technologies that ensure seamless and error-free production. By automating the roll forming process, our machines guarantee consistent quality, precise dimensions, and tight tolerances, resulting in flawless metal roofing sheets every time.One of the key advantages of our trapezoidal panel roll forming machines is their versatility. They can produce a wide range of roofing and cladding profiles, catering to different design preferences and architectural requirements. Whether you need corrugated sheets, standing seam panels, or any other trapezoidal profiles, our machines can accommodate your diverse production needs, ensuring utmost customer satisfaction.Furthermore, our trapezoidal panel roll forming machines are designed with utmost safety considerations. They are equipped with safety features such as emergency stop buttons, safety guards, and sensors to prevent accidents and ensure the well-being of your operators. Additionally, our machines are operator-friendly, with user-friendly interfaces and easy-to-understand controls, making the production process efficient and hassle-free.In conclusion, if you are in the market for a reliable and efficient trapezoidal panel roll forming machine, look no further than our product range. With our cutting-edge technology, versatile production capabilities, and commitment to excellence, we provide you with the best solution for your metal roofing and cladding needs. Our machines ensure consistent quality, precise dimensions, and exceptional performance, delivering outstanding results every time. Invest in our trapezoidal panel roll forming machines, and elevate the standards of your roofing and cladding projects.